Discover
Augmented Ops
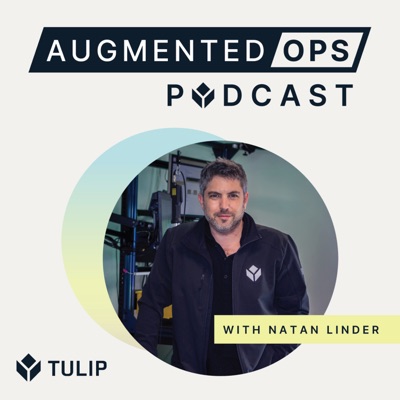
Augmented Ops
Author: Tulip
Subscribed: 27Played: 1,025Subscribe
Share
© 2024 Tulip Interfaces
Description
Augmented Ops is a podcast for industrial leaders, shop floor operators, citizen developers, and anyone else that cares about what the future of frontline operations will look like across industries. We equip our listeners with the knowledge to understand the latest advancements at the intersection of manufacturing and technology, as well as actionable insights that they can implement in their own operations. This show is presented by Tulip, the Frontline Operations Platform.
143 Episodes
Reverse
This week’s guest is Kence Anderson (https://www.linkedin.com/in/kence), CEO of Composabl.
Kence and Natan explore the role of AI agents in industrial processes, how manufacturers are using them to solve complex problems like scheduling or machine control, and the challenges of building startups in the manufacturing space. Kence also lays out how his concept of machine teaching differs from traditional machine learning techniques, and why he believes in taking a composable approach to building solutions for problems on the shop floor.
Augmented Ops is a podcast for industrial leaders, citizen developers, shop floor operators, and anyone else that cares about what the future of frontline operations will look like across industries. This show is presented by Tulip (https://tulip.co/), the Frontline Operations Platform. You can find more from us at Tulip.co/podcast (https://tulip.co/podcast) or by following the show on LinkedIn (https://www.linkedin.com/company/augmentedpod/). Special Guest: Kence Anderson.
This week’s guest is Fabio Violante (https://www.linkedin.com/in/fabioviolante), CEO of Arduino.
Fabio and Natan explore the importance of open source technology in manufacturing and how the democratization of embedded systems development is reshaping the industry. Fabio also shares the history of Arduino, and how he led the charge to evolve their approach from focusing purely on makers and hobbyists, to supporting enterprise grade applications with a new line of hardware.
Augmented Ops is a podcast for industrial leaders, citizen developers, shop floor operators, and anyone else that cares about what the future of frontline operations will look like across industries. This show is presented by Tulip (https://tulip.co/), the Frontline Operations Platform. You can find more from us at Tulip.co/podcast (https://tulip.co/podcast) or by following the show on LinkedIn (https://www.linkedin.com/company/augmentedpod/). Special Guest: Fabio Violante.
This week’s guest is Kevin Kidd (https://www.linkedin.com/in/kevin-kidd-5ab572113/), Director of Software and Analytics at RFK Racing.
While advanced manufacturing might not be the first thought that comes to mind when you hear the word NASCAR, Kevin sheds light on the complex processes and digital tools that go into building high performance race cars. He also explains how citizen development helped the team go from running on Excel to building the custom software they need, as well as the key role that data governance and advanced analytics play in putting a car that’s ready to win out on the track every week.
Augmented Ops is a podcast for industrial leaders, citizen developers, shop floor operators, and anyone else that cares about what the future of frontline operations will look like across industries. This show is presented by Tulip (https://tulip.co/), the Frontline Operations Platform. You can find more from us at Tulip.co/podcast (https://tulip.co/podcast) or by following the show on LinkedIn (https://www.linkedin.com/company/augmentedpod/). Special Guest: Kevin Kidd.
This week’s guest is Marc Nash (https://www.linkedin.com/in/marcnash1/), SVP of Operations and R&D at Outset Medical.
In an industry dominated by legacy players, Marc explains how Outset set out to redefine what is possible when it comes to patient health, and how they leveraged an equally disruptive approach to manufacturing to give them a competitive edge. He also explains how they are taking advantage of IoT to improve their products even after they have been shipped, the evolution of lean manufacturing in the digital age, and the value of composability in developing next-gen production systems.
Augmented Ops is a podcast for industrial leaders, citizen developers, shop floor operators, and anyone else that cares about what the future of frontline operations will look like across industries. This show is presented by Tulip (https://tulip.co/), the Frontline Operations Platform. You can find more from us at Tulip.co/podcast (https://tulip.co/podcast) or by following the show on LinkedIn (https://www.linkedin.com/company/augmentedpod/). Special Guest: Marc Nash.
This week, Natan Linder (https://www.linkedin.com/in/linder/), Co-Founder and CEO of Tulip (https://tulip.co/) sits down with Tulip CMO Madilynn Castillo (https://www.linkedin.com/in/madilynncastillo/) to reflect on the second annual Operations Calling conference and what it means for the future of frontline operations.
Natan and Madi discuss what makes Operations Calling more than just another user conference, the importance of authenticity, and building a community around frontline operations. They also explain what it takes to build an operations-first ecosystem, how the industry is evolving, and how they’re planning next year’s Operations Calling.
Augmented Ops is a podcast for industrial leaders, citizen developers, shop floor operators, and anyone else that cares about what the future of frontline operations will look like across industries. This show is presented by Tulip (https://tulip.co/), the Frontline Operations Platform. You can find more from us at Tulip.co/podcast (https://tulip.co/podcast) or by following the show on LinkedIn (https://www.linkedin.com/company/augmentedpod/). Special Guest: Madilynn Castillo.
This week’s guest is Daniele Iacovelli (https://www.linkedin.com/in/daniele-iacovelli-8684a9b2/), SVP, Global Head of Digital, Analytics (AI) & Operational Excellence at Roche.
Although regulated industries like pharmaceutical manufacturing can be slow to digitally transform their manufacturing operations, Daniele lays out how changing trends in the industry have led Roche to architect a new digital production system, with a focus on a composable, future-proof architecture. He also lays out how rapid solution development enabled by new software platforms and a citizen developer approach is enabling people across the company to solve their own problems, while also laying the groundwork for rethinking the traditional software validation approach that dominates regulated industries. Plus, what the role of GenAI should be in a GxP environment, and more.
Augmented Ops is a podcast for industrial leaders, citizen developers, shop floor operators, and anyone else that cares about what the future of frontline operations will look like across industries. This show is presented by Tulip (https://tulip.co/), the Frontline Operations Platform. You can find more from us at Tulip.co/podcast (https://tulip.co/podcast) or by following the show on LinkedIn (https://www.linkedin.com/company/augmentedpod/). Special Guest: Daniele Iacovelli.
This week’s guest is Rick Bullotta (https://www.linkedin.com/in/rickbullotta/), longtime veteran of the industrial software space and co-founder of Lighthammer and Thingworx.
Rick and Natan explore the history of MES solutions, how Frontline Operations Platforms are democratizing the development of industrial software, and what this means for the future architecture of the manufacturing tech stack. They also break down the hype vs. reality in industrial AI, and discuss which use cases continue to require a human-in-the-loop.
Augmented Ops is a podcast for industrial leaders, citizen developers, shop floor operators, and anyone else that cares about what the future of frontline operations will look like across industries. This show is presented by Tulip (https://tulip.co/), the Frontline Operations Platform. You can find more from us at Tulip.co/podcast (https://tulip.co/podcast) or by following the show on LinkedIn (https://www.linkedin.com/company/augmentedpod/). Special Guest: Rick Bullotta.
In this bonus episode, Elisabeth Reynolds—MIT Professor of the Practice, former White House policymaker, and now Strategic Advisor to Tulip—joins Natan Linder to discuss the building momentum around reindustrialization in the United States.
Liz calls attention to the most important factors shaping the industrial landscape, and the need for a clear national strategy that can direct government coordination with manufacturers. Liz also explores the challenges in introducing software to the frontline workforce, ways manufacturers can address skill gaps, and the role of venture capital in fueling innovation.
Rendustrialize Summit (https://www.axios.com/2024/07/01/us-industry-leadership-summit-detroit)
Reindustrialize Manifesto (https://www.reindustrialize.com/resources/manifesto)
SCSP Advanced Manufacturing Report (https://www.scsp.ai/wp-content/uploads/2024/06/Advanced-Manufacturing-Action-Plan.pdf)
Augmented Ops is a podcast for industrial leaders, shop floor operators, citizen developers, and anyone else that cares about what the future of frontline operations will look like across industries. This show is presented by Tulip (https://tulip.co/), the Frontline Operations Platform. You can find more from us at Tulip.co/podcast (https://tulip.co/podcast) or by following the show on LinkedIn (https://www.linkedin.com/company/augmentedpod/). Special Guest: Elisabeth Reynolds.
This week marks the final episode of Season 1 of Augmented Ops! Natan Linder and Erik Mirandette sit down to discuss their takeaways from the first season—while trying not to get derailed analogizing frontline operations to the Celtics Championship win.
Natan and Erik highlight the advancements (and stumbles) in industrial AI, and the way that open, interoperable ecosystems have fundamentally changed the way manufacturing tech stacks are built. They also reflect the need to focus on the frontline worker, the power of democratizing advanced technology, and more.
Augmented Ops is a podcast for industrial leaders, shop floor operators, citizen developers, and anyone else that cares about what the future of frontline operations will look like across industries. This show is presented by Tulip (https://tulip.co/), the Frontline Operations Platform. You can find more from us at Tulip.co/podcast (https://tulip.co/podcast) or by following the show on LinkedIn (https://www.linkedin.com/company/augmentedpod/).
This week’s guest is Jeff Kramer (https://www.linkedin.com/in/jeffrey-kramer-a367906/), VP Technology & Digital Factory at Kason Industries (https://www.kasonind.com/).
Jeff discusses why manufacturers struggle to develop a cohesive digital strategy, and lays out best practices around governance, data architecture, and bridging the IT/OT divide. He also explains why it’s critical for organizations to empower their frontline personnel by using technology to enable a citizen developer approach.
Augmented Ops is a podcast for industrial leaders, shop floor operators, citizen developers, and anyone else that cares about what the future of frontline operations will look like across industries. This show is presented by Tulip (https://tulip.co/), the Frontline Operations Platform. You can find more from us at Tulip.co/podcast (https://tulip.co/podcast) or by following the show on LinkedIn (https://www.linkedin.com/company/augmentedpod/). Special Guest: Jeff Kramer.
This week’s guest is Kai Yang (https://www.linkedin.com/in/kaiyangtw/), VP of Product at LandingAI (https://landing.ai/).
Kai discusses the need for a data-centric approach to AI, why vendors should build tools rather than solutions, and more, sharing lessons learned from his career in machine learning and software development. He also explains how new tools like visual prompting are democratizing computer vision and enabling anyone, regardless of skill level, to develop their own machine learning models.
Augmented Ops is a podcast for industrial leaders, shop floor operators, citizen developers, and anyone else that cares about what the future of frontline operations will look like across industries. This show is presented by Tulip (https://tulip.co/), the Frontline Operations Platform. You can find more from us at Tulip.co/podcast (https://tulip.co/podcast) or by following the show on LinkedIn (https://www.linkedin.com/company/augmentedpod/). LandingAI is a Tulip Technology Ecosystem (https://tulip.co/partners/technology-ecosystem-partners/) Partner. Special Guest: Kai Yang.
This week’s guest is Anna Shedletsky (https://www.linkedin.com/in/annakatrinashedletsky/), Co-Founder and CEO of Instrumental (https://instrumental.com/).
Having started her career as an engineer at Apple, Anna shares lessons around quality management, which manufacturing KPIs actually matter, and how to take an idea from prototype to production. Plus, she lays out why organizations should think about manufacturing as a profit generator rather than a cost center, and why being able to demonstrate ROI is vital for engineers to advocate for the tech they need.
Augmented Ops is a podcast for industrial leaders, shop floor operators, citizen developers, and anyone else that cares about what the future of frontline operations will look like across industries. This show is presented by Tulip (https://tulip.co/), the Frontline Operations Platform. You can find more from us at Tulip.co/podcast (https://tulip.co/podcast) or by following the show on LinkedIn (https://www.linkedin.com/company/augmentedpod/). Instrumental is a Tulip Technology Ecosystem (https://tulip.co/partners/technology-ecosystem-partners/) Partner. Special Guest: Anna Shedletsky.
This week, Natan Linder (https://www.linkedin.com/in/linder/), Co-Founder and CEO of Tulip (https://tulip.co/) sits down with Madilynn Castillo (https://www.linkedin.com/in/madilynncastillo/), Head of Marketing for a recap of their experiences at this year’s Hannover Messe — the world’s largest industrial trade fair.
They explore the lackluster state of AI in industrial software, the rise of composable software architectures, and how open technology ecosystems are becoming the norm throughout the industry. Plus, an overview of the latest developments from Tulip that debuted at the show.
Augmented Ops is a podcast for industrial leaders, shop floor operators, citizen developers, and anyone else that cares about what the future of frontline operations will look like across industries. This show is presented by Tulip (https://tulip.co/), the Frontline Operations Platform. You can find more from us at Tulip.co/podcast (https://tulip.co/podcast) or by following the show on LinkedIn (https://www.linkedin.com/company/augmentedpod/). Special Guest: Madilynn Castillo.
This week’s guest is Matt Lowe (https://www.linkedin.com/in/mwlowe/), Co-Founder and CEO of ZeroKey (https://zerokey.com/).
Not only is he a contributor to major open source projects like Linux and Arduino, Matt is the inventor of Quantum RTLS, a system that uses ultrasound to achieve 3D position tracking of objects with an unmatched level of fidelity. He explains what makes ultrasound-based positioning systems ideal for manufacturing environments, how spatial intelligence offers new ways to solve problems on the shop floor, and how open architecture can eliminate the need for system integrators.
Augmented Ops is a podcast for industrial leaders, shop floor operators, citizen developers, and anyone else that cares about what the future of frontline operations will look like across industries. This show is presented by Tulip (https://tulip.co/), the Frontline Operations Platform. You can find more from us at Tulip.co/podcast (https://tulip.co/podcast) or by following the show on LinkedIn (https://www.linkedin.com/company/augmentedpod/). ZeroKey is a Tulip Technology Ecosystem (https://tulip.co/partners/technology-ecosystem-partners/) Partner. Special Guest: Matt Lowe.
This week’s guest is Dominik Obermaier (https://www.linkedin.com/in/dobermai/), Co-Founder and CTO of HiveMQ (https://www.linkedin.com/company/hivemq-gmbh/).
With over 10 years of experience serving on the MQTT technical committee and helping organizations build their data foundations using HiveMQ’s MQTT platform, Dominik shares his deep expertise on the technology. He explains what makes MQTT such an important communications protocol, why the emergence of the Unified Namespace matters for manufacturers, and debates the merits of on-prem vs. cloud solutions.
Augmented Ops is a podcast for industrial leaders, shop floor operators, citizen developers, and anyone else that cares about what the future of frontline operations will look like across industries. This show is presented by Tulip (https://tulip.co/), the Frontline Operations Platform. You can find more from us at Tulip.co/podcast (https://tulip.co/podcast) or by following the show on LinkedIn (https://www.linkedin.com/company/augmentedpod/). HiveMQ is a Tulip Technology Ecosystem (https://tulip.co/partners/technology-ecosystem-partners/) Partner. Special Guest: Dominik Obermaier.
This week’s guest is Jay Lee (https://www.linkedin.com/in/jay-lee-116ba59/), Director of the Industrial AI Center at the University of Maryland (https://www.linkedin.com/school/university-of-maryland/).
Dr. Lee shares his experiences from the early days programming machines with punch cards, to eventually developing advanced machine learning applications for industry. He explains how AI and ML are reshaping manufacturing, the workforce, and global supply chains. Plus, he lays out his vision for how our education system needs to change in order to train the next generation of AI practitioners.
Augmented Ops is a podcast for industrial leaders, shop floor operators, citizen developers, and anyone else that cares about what the future of frontline operations will look like across industries. This show is presented by Tulip (https://tulip.co/), the Frontline Operations Platform. You can find more from us at Tulip.co/podcast (https://tulip.co/podcast) or by following the show on LinkedIn (https://www.linkedin.com/company/augmentedpod/). Special Guest: Jay Lee.
This week’s guest is Alex Krüger (https://www.linkedin.com/in/alexander-krueger/), Co-founder and CEO of United Manufacturing Hub (https://www.linkedin.com/company/united-manufacturing-hub/), or UMH.
Alex shares his journey from working on integration projects in consulting fresh out of college, to founding UMH and building an open source alternative to the offerings from incumbent vendors. He breaks down the role of the open source software movement in manufacturing, how the Unified Namespace architecture compares to the traditional ISA-95 model, and how IT can best enable OT to solve problems. Plus, he shares his vision for how microservice-based MES solutions can disrupt the existing monolithic applications.
Augmented Ops is a podcast for industrial leaders, shop floor operators, citizen developers, and anyone else that cares about what the future of frontline operations will look like across industries. This show is presented by Tulip (https://tulip.co/), the Frontline Operations Platform. You can find more from us at Tulip.co/podcast (https://tulip.co/podcast) or by following the show on LinkedIn (https://www.linkedin.com/company/augmentedpod/). UMH is a Tulip Technology Ecosystem (https://tulip.co/partners/technology-ecosystem-partners/) Partner. Special Guest: Alex Krüger.
This week’s guest is Vatsal Shah (https://www.linkedin.com/in/vatsal12/), Founder and CEO of Litmus (https://www.linkedin.com/company/litmus-automation/).
Vatsal discusses his journey from an automation engineer at Rockwell, to building a new industrial data platform from the ground up after becoming frustrated with the limitations of the offerings from established vendors. He discusses manufacturers’ exodus from on-prem to cloud systems, the pros and cons of data protocols like MQTT and Sparkplug B, and why the Unified Namespace architecture is getting so much attention. Plus, he shares his vision for the future of edge computing and how an open ecosystem of interoperable tools is transforming the industry.
Augmented Ops is a podcast for industrial leaders, shop floor operators, citizen developers, and anyone else that cares about what the future of frontline operations will look like across industries. This show is presented by Tulip (https://tulip.co/), the Frontline Operations Platform. You can find more from us at Tulip.co/podcast (https://tulip.co/podcast) or by following the show on LinkedIn (https://www.linkedin.com/company/augmentedpod/). Litmus is a Tulip Technology Ecosystem (https://tulip.co/partners/technology-ecosystem-partners/) Partner. Special Guest: Vatsal Shah.
This week’s guest is Dr. Lisa Graham (https://www.linkedin.com/in/lisagraham2/), CEO of Seeq (https://www.linkedin.com/company/seeqcorporation/).
Dr. Graham discusses her journey from process engineer, to using Seeq’s platform as a customer, and now leading the company as CEO. Drawing on her extensive experience in operations, she discusses how advanced analytics, generative AI, and the emergence of an interoperable technology ecosystem are reshaping industries. Plus, she shares best practices for IT/OT collaboration, her vision for the future of historians, and how the democratization of data science is paving the way for a more efficient and sustainable future in operations and manufacturing.
Augmented Ops is a podcast for industrial leaders, shop floor operators, citizen developers, and anyone else that cares about what the future of frontline operations will look like across industries. This show is presented by Tulip (https://tulip.co/), the Frontline Operations Platform. You can find more from us at Tulip.co/podcast (https://tulip.co/podcast) or by following the show on LinkedIn (https://www.linkedin.com/company/augmentedpod/). Seeq is a Tulip Technology Ecosystem (https://tulip.co/partners/technology-ecosystem-partners/) Partner. Special Guest: Lisa Graham.
This week’s guest is Jeff Winter (https://www.linkedin.com/in/jeffreyrwinter/), Sr. Director of Industry Strategy for Manufacturing at Hitachi Solutions (https://www.linkedin.com/company/hitachi-solutions-america/).
Jeff offers his insights into the history of the Industry 4.0 movement and how he expects it to evolve in the coming years. His discussion highlights the balance between AI and human ingenuity, the role of frontline workers in an increasingly automated manufacturing environment, and the untapped potential of manufacturing data.
Augmented Ops is a podcast for industrial leaders, shop floor operators, citizen developers, and anyone else that cares about what the future of frontline operations will look like across industries. This show is presented by Tulip (https://tulip.co/), the Frontline Operations Platform. You can find more from us at Tulip.co/podcast (https://tulip.co/podcast) or by following the show on LinkedIn (https://www.linkedin.com/company/augmentedpod/). Special Guest: Jeff Winter.
Comments
Top Podcasts
The Best New Comedy Podcast Right Now – June 2024The Best News Podcast Right Now – June 2024The Best New Business Podcast Right Now – June 2024The Best New Sports Podcast Right Now – June 2024The Best New True Crime Podcast Right Now – June 2024The Best New Joe Rogan Experience Podcast Right Now – June 20The Best New Dan Bongino Show Podcast Right Now – June 20The Best New Mark Levin Podcast – June 2024