Discover
Design World
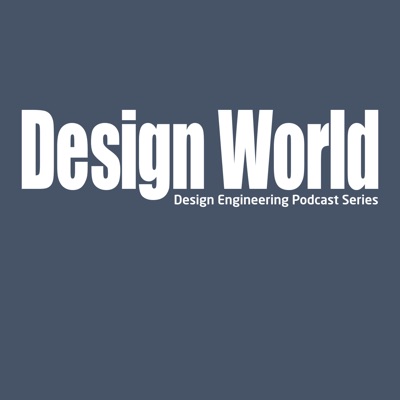
Design World
Author: Design World
Subscribed: 828Played: 3,920Subscribe
Share
© All rights reserved
Description
Design World serves design engineers, engineering managers and other professionals in industrial segments including factory automation, robotics, rapid prototyping, semiconductor, material handling, packaging, medical equipment and devices.
188 Episodes
Reverse
Modern machine design is all about delivering higher performance at a lower cost with higher reliability. Delivering these often-conflicting performance characteristics is the mark of a great designer, and for the most common form of industrial motion, rotation, newer applications such as SCARA robots and their end effectors need torque with low mass in the smallest possible footprint. Frameless motors are an ideal choice for applications that are space-limited or must strictly control inertial mass. Kollmorgen frameless motor expert Tom Wood discusses the technology in conversation with Jim Anderton in this podcast.
The Engineering Research Visioning Alliance (ERVA) published a report on Engineering the Future of Distributed Manufacturing and identifies priorities that can revitalize U.S. manufacturing with sustainability and resilience in mind. In this podcast, Tali Rosman, startup advisor and Entrepreneur-at-Residence at Toronto Metropolitan University, shares how 3D printing plays a role in ERVA’s vision. Tali has worked at Stratasys, led Xerox’s former 3D printing subsidiary, Elem Additive, and now serves as a business advisor with expertise in advanced manufacturing.
Electrostatic discharge (ESD) within precision additive manufacturing by Design World
Micro tools play a critical role in the manufacturing of medical devices, microelectronics, semiconductors, and any miniature component where precision is essential. Darren Fox, a product manager at ANCA with over 33 years of experience in the cutting tool industry, discusses ultra-precision grinding and ANCA's FX7 Ultra.
In this episode of Design World’s Technology Tuesdays Podcast, VP, Editorial Director Paul J. Heney chats about vision systems with Philip Freidin, an Applications Engineer with IDS Imaging Development Systems Inc. They discuss new and interesting applications, how to select the best industrial camera system, and what the future holds for this important technology area.
In our latest Technology Tuesdays podcast, Design World’s Michelle Froese speaks with David Church, president of Sorbothane, about innovative shock and vibration solutions. Sorbothane has been developing materials and components that isolate vibration, attenuate shock, and damp unwanted noise for more than 40 years.
In our latest Technology Tuesdays podcast, Design World’s Michelle Froese speaks with Mitsubishi Electric Automation’s product marketing manager for mechatronics and robotics, Patrick Varley.
In this discussion, we delve into the topic of robotic automation and software provider solutions — and, specifically, how this combination can help ease labor shortages. Patrick explains the significance of consumer personalization and how advanced technology from leading innovators can address the contemporary issues facing today’s manufacturers.
Copper is viewed as a material that will accelerate future aerospace production. For example, the privately funded company Ursa Major delivered a copper-based 3D-printed rocket engine combustion chamber from its additive manufacturing lab in Youngstown, Ohio. A challenge, however, is that the existing supply chain for high temperature metal alloy components is limited. However, development continues.
Several engineering companies say we have the technology to reverse climate change, one of which is using direct air capture. Interestingly, additive manufacturing has the potential to play a major role here.
In our latest Technology Tuesday’s podcast, Design World’s Michelle Froese speaks with David Church, president of Sorbothane, about innovative shock and vibration solutions. Sorbothane has been developing materials and components that isolate vibration, attenuate shock, and damp unwanted noise for 40 years. In fact, the company is celebrating four decades in business this year!
In our latest Technology Tuesday’s podcast, Design World’s Michelle Froese speaks with David Church, president of Sorbothane, about innovative shock and vibration solutions. Sorbothane has been developing materials and components that isolate vibration, attenuate shock, and damp unwanted noise for 40 years. In fact, the company is celebrating four decades in business this year!
In honor of Sorbothane’s anniversary, we discuss the unique history of the company, including how the material was developed for insoles to support runners and then became essential for industrial industries to protect vital cargo and equipment. We also cover Sorbothane material’s properties, the company’s new standard products (launching this fall), and how its online Design Guide Calculators can support your application.
Some of the materials used in 3D printing are generally either not very, or even not degradable in the environment. Some developers and manufacturers though, are working to develop materials that are more eco-friendly, as well as delivering the mechanical properties designers look for. Here is an interview with Dr. Raymond Weitekamp, founder of the Berkeley-based 3D printing startup, polySpectra.
3D printing/additive manufacturing can help designers simplify a part, reducing assembly steps in many cases, and creating a better end product. Is it possible, though, to over engineer a part? Here are some tips to help reduce excessive engineering and get parts out to market faster.
The supply chain continues to be a story for additive manufacturing, especially with the recent news from President Biden on the new AM Forward initiative. I recently interviewed Dave Evans, CEO of Fictiv, to discuss AM and the supply chain, among other subjects.
A conversation with Jeff Blanford, a Solution Architect at Morf3D, to discuss the latest developments with additive technology. This conversation shifted to looking at additive technology as more of a digital enabling technology, not just a different way to build parts.
The scale of sizes that 3D printing machines can handle is impressive, from huge wind turbine blades to parts that are small, such as two microns. John Kawola, CEO of Boston Micro Fabrication discusses the microscale side of 3D printing.
Recently, the World Economic Forum, in collaboration with ETH Zurich and Fraunhofer IGCV, IPT and IAPT, released a report on the current state of additive manufacturing (AM) and its future. Their goal was to provide a realistic understanding of what AM can deliver today and why some are achieving that potential while others are not, as well as define the most probable near-term future production scenarios and what needs to happen to make those scenarios a reality. Pat Carey, Senior Vice President of Strategic Growth for Stratasys addresses this subject.
As additive technology gains importance in aerospace innovation, it offers compelling opportunities to revolutionize critical elements of the aerospace workflow. From design to certification and to production, AM helps companies unlock innovation and maximize efficiency while maintaining the high levels of quality required for aerospace applications.
Additive hardware continues to improve in productivity, accuracy, and in ease of use. Now, the focus is on software to improve additive functions and capabilities, and to take additive to the next level.
As AM becomes more accepted as part of a manufacturing supply chain, it is altering the way engineers work and develop products. We recently had a conversation with Daniel Lazier, product marketing manager at Markforged.
Top Podcasts
The Best New Comedy Podcast Right Now – June 2024The Best News Podcast Right Now – June 2024The Best New Business Podcast Right Now – June 2024The Best New Sports Podcast Right Now – June 2024The Best New True Crime Podcast Right Now – June 2024The Best New Joe Rogan Experience Podcast Right Now – June 20The Best New Dan Bongino Show Podcast Right Now – June 20The Best New Mark Levin Podcast – June 2024
For me, you should probably think about the fact that you need any work on metal, for instance, the same metal cutting, and contact the professionals for assistance at once. I myself have done so, I suggest looking here for sheet metal processing https://magnet.com.ua/en/ They helped me and they cut filigree. I didn't even expect it, so I suggest reading this detail.
this is my first podcast from Design World. Great topic, and great conversation. Can you put some cloth on the walls? It sounds like you're talking in a bowl.
Great topics but not so great audio control. The variants in sound volume is roughly 10 to 20% at the start and end of every episode.