Discover
Digital Transformation by Siemens Digital Industries
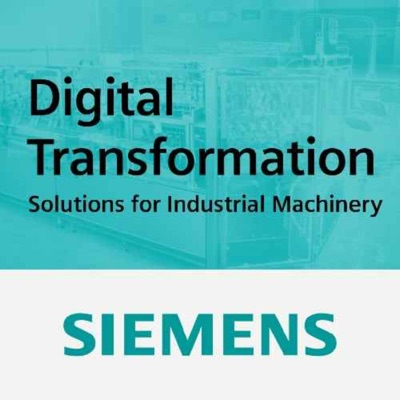
Digital Transformation by Siemens Digital Industries
Author: Siemens Digital Industries
Subscribed: 52Played: 587Subscribe
Share
© Siemens Digital Industries
Description
This Smart Manufacturing Podcast by Siemens Digital Industries explores the advantages of smart manufacturing, a digitalized product development strategy and the solutions it offers for the Industrial Machinery industry.
42 Episodes
Reverse
As we've learned throughout this podcast series, industrial machinery manufacturers have seen groundbreaking technological advancements in the areas of design and machine simulation.
In the first three podcasts, we talked about the evolution of technology within the machinery industry, key trends that continue to shape the industry today, and we have also introduced the Advanced Machine Engineering solution at a high level by describing two of the three key differentiators: multi-disciplinary design and virtual machine simulations & commissioning.
Today, in our final podcast of the series, Bill and I are discussing the third key differentiator of the Advanced Machine Engineering solution – multi-disciplinary Bill of Material and configuration management.
Bill Davis is the Director of Industrial Machinery & Heavy Equipment Solutions at Siemens Digital Industries Software, working to help industrial machinery customers and heavy equipment customers improve innovation and profitability through the application of the Siemens portfolio. His background is in automation, converting, and packaging machinery. His 30 years of experience in engineering and management positions have shaped how he helps their customers and their go-to-market strategy.
So, listen to Episode 4 of the Siemens Podcast on Advanced Machine Engineering, to learn how to leverage your proprietary data to create a digital thread approach to engineering and also create a competitive advantage.
Questions I ask:
What is a managed environment and why should it be important to the machine builders and their suppliers? (02:15)
Is complexity the only challenge around this topic of data management, or are there other areas that we need to be concerned with, as well? (07:31)
How can Advanced Machine Engineering solution help solve these challenges? (10:25)
Before we end this podcast, could you quickly summarize the main advantages of the Advanced Machine Engineering solution and why it should be considered by our listeners? (14:58)
In this episode, you will learn:
The Configure to Order approach. (03:48)
The Engineer to Order approach. (04:46)
The importance of having a Bill of Material that represents the entire machine. (05:57)
Connect with Bill:
LinkedIn
Hosted on Acast. See acast.com/privacy for more information.
In our last two podcasts, we talked about the evolution of technology within the machinery industry, key trends that continue to shape the industry today, and we introduced the Advanced Machine Engineering solution at a high level by taking a deep dive into one of the three key differentiators - multi-disciplinary design.
Today, our expert in the series, Bill, focuses the discussion around virtual machine simulation and commissioning and how machine manufacturers are implementing this approach to improve the quality and reduce delivery time for highly complex machines.
Bill Davis is the Director of Industrial Machinery & Heavy Equipment Solutions at Siemens Digital Industries Software, working to help industrial machinery customers and heavy equipment customers improve innovation and profitability through the application of the Siemens portfolio. His background is in automation, converting, and packaging machinery. His 30 years of experience in engineering and management positions have shaped how he helps their customers and their go-to-market strategy.
So, listen to Episode 3 of the Siemens Podcast on Advanced Machine Engineering, where we talk about the importance of adopting and integrating virtual machine simulation and commissioning into the manufacturing process.
Questions I ask:
What is virtual machine simulation and commissioning? (01:51)
What are the simulation approaches that are being leveraged to address the challenges? (08:01)
What are some of the benefits for the manufacturers that incorporate this virtual machine simulation and commissioning approach and integrate it into their manufacturing process? (16:16)
In this episode, you will learn:
The challenges that machine builders are currently facing. (03:21)
The advantages of simulating the machine’s performance in a virtual world. (13:53)
Connect with Bill:
LinkedIn
Hosted on Acast. See acast.com/privacy for more information.
In our last podcast, we talked about the evolution of technology within the machinery industry and we highlighted three key differentiators for advanced machine engineering solutions: multi-disciplinary design, virtual machine simulation and commissioning, and multi-disciplinary BOM and configuration management.
Today, in our second podcast of this series, we are discussing the first key differentiator and we are learning how machine manufacturers are leveraging multi-disciplinary design to make their manufacturing more efficient.
Bill Davis is the Director of Industrial Machinery & Heavy Equipment Solutions at Siemens Digital Industries Software, working to help industrial machinery customers and heavy equipment customers improve innovation and profitability through the application of the Siemens portfolio. His background is in automation, converting, and packaging machinery. His 30 years of experience in engineering and management positions have shaped how he helps their customers and their go-to-market strategy.
So, listen to the second part of the Siemens Podcast on Advanced Machine Engineering, where we discuss the significance of multi-disciplinary collaboration for machine builders and we also expand on the benefits of implementing this approach.
Questions I ask:
What exactly is multi-disciplinary design? (01:55)
How would you respond to someone who might minimize the value that you just described for multi-disciplinary collaboration? (04:28)
Do you have any examples for any companies that have embraced Advanced Machine Engineering as a strategy and if so, what kind of results they might have seen? (14:08)
In this episode, you will learn:
The meaning of the Mechatronics Concept Designer. (06:59)
The dangers of having too much integration too quickly. (08:01)
The benefits for those who are incorporating a multi-disciplinary collaboration into their manufacturing process. (10:47)
Connect with Bill:
LinkedIn
Hosted on Acast. See acast.com/privacy for more information.
It is a daunting task to design, validate, and manage modern industrial machinery to address rapidly increasing automation complexity and mass customization requirements while increasing market share and unlocking new business opportunities.
Today, in our first podcast of the series, we are discussing how machinery manufacturers are gaining a competitive advantage by implementing a digital twin approach to engineering, which enables the development of highly complex machines faster.
Bill Davis is the Director of Industrial Machinery & Heavy Equipment Solutions at Siemens Digital Industries Software, working to help industrial machinery customers and heavy equipment customers improve innovation and profitability through application of the Siemens portfolio. His background is in automation, converting, and packaging machinery. His 30 years of experience in engineering and management positions have shaped how he helps their customers and their go-to-market strategy.
So, listen to the first part of this Siemens Podcast on Advanced Machine Engineering, where we will cover some of the challenges and trends facing machinery manufacturers today, and how these challenges are driving an evolution of technology that is now enabling machine manufacturers with the ability to maximize profits and also look at the industry trends driving the adoption of this innovative technology.
Questions I ask:
Let's take a look back at the last 10 years. There have been so many changes in the machinery industry, but what would you cite, from your perspective, as one or two significant technology changes that have shaped the industry in the past decade? (03:52)
Would you say technology has been the biggest catalyst for change in the machinery industry? Or are there other factors that are creating the need for advanced technology solutions as well? (05:58)
Can you, from your perspective, elaborate a bit on the concept of digitalization and more specifically, the digital twin in the context of the industrial machinery? (09:11)
Can you help the listeners understand what exactly is Advanced Machine Engineering, and what makes it unique from any other approaches machine builders and their suppliers are using today? (12:23)
In this episode, you will learn:
About Bill’s background and how that has helped him with his current role at Siemens. (01:42)
The meaning of Generative Design Movement. (04:50)
How the consumer-driven customization influences machine manufacturing. (06:27)
Why you should adopt a digital twin, from a machinery standpoint. (10:43)
Connect with Bill:
LinkedIn
Hosted on Acast. See acast.com/privacy for more information.
With technological advancements all around us in the manufacturing industry, it's important to understand how improving machinery operations is dependant upon making your factory smarter.
Today, in our fourth and final podcast of these series, Bill Davis — the Director of Industrial Machinery and Heavy Equipment Solutions at Siemens — and I, we're discussing the smart manufacturing techniques to use to improve machine assembly, shop layouts, and process simulation.
So, listen to the Final Episode of Siemens PLM Podcast series, to learn how to be more efficient in terms of generating more cash and reducing the quality problems overall, with the help of the digital twin.
In this episode, you will learn:
How to make sure you get the right parts to the right spot on the assembly floor at the right time. (01:53)
Why process simulation is important for continuous improvement. (02:55)
Why scheduling machines and multiple product lines at the same time is as important as the individual assembly process. (05:12)
What you can do to bring a machine into the commissionable state as quickly as possible so that you don’t have idle time for your cash. (06:30)
Examples of use cases where companies have implemented the simulation and seen a reduction in errors and time, while an increase in cash flow. (09:49)
What closed-loop quality is and how does it work. (14:29)
Hosted on Acast. See acast.com/privacy for more information.
Innovations with industrial machinery and manufacturing are seeing groundbreaking technological advancements.
There are not many companies the size of Siemens with both the manufacturing capability and their industry breadth of knowledge.
Today we're learning how machine manufacturers are implementing smart manufacturing to improve the product of parts manufacturing.
Listen to the Third Episode of Siemens PLM Podcast series, where Bill and I are going to take a close inspection of the improvement smart manufacturing brings to manufacturing execution management, including manufacturing of the bill of process, and manufacturing of the bill of materials.
Questions I ask:
When you look at the greater global Siemens and their approach to smart manufacturing, could you give some of the things we have learned in our approach, and how that's changed and how it's been a dynamic process of learning and improving and just our general philosophy in approaching smart manufacturing? (01:25)
When you spoke of quality, when we're looking at building the highest quality parts for the lowest amount of labor content in the fastest time, what are some of the differentiators that Siemens provides in parts manufacturing? What kind of technology are we inputting to make sure that happens? (08:13)
When you're talking about these complex machine centers, how we can be smarter and the challenges of manufacturing operations to maximize quality in assembly and in commissioning, what are some of the right solutions that we use in implementing that?
In this episode, you will learn:
What the concept “Bill of Process” means. (04:53)
The importance of meeting the conditions that the machine shop has, when fabricating any part of the machine (08:56)
The implications of moving away from single-purpose machining centers toward higher capacity multi-function machining centers. (13:40)
How Siemens is dealing with the skilled labor shortage. (15:10)
Hosted on Acast. See acast.com/privacy for more information.
What’s the digital twin really being used for?
In this podcast, Bill Davis—the Director of Industrial Machinery and Heavy Equipment Solutions at Siemens—and I do a deep-dive into how machine manufacturers leverage the digital twin technology to start utilizing smart manufacturing. The digital twin does more than what one sees on the surface; it really spans the whole gamut, from design to manufacturing to operations management, into commissioning and service life.
Tune in to learn about the portability of this tool, and how the digital twin overall vastly improves the production process.
Some Questions I Ask:
How does 3-D printing come into play with Smart Manufacturing? (1:31)
What are the benefits of smart manufacturing? (10:29)
In This Episode, You Will Learn:
What the digital twin fully encompasses and how it functions in the design process. (4:06)
How the digital twin is applied to manufacturing disciplines. (6:26)
What factors determine the overall return on investment in smart manufacturing. (10:47)
Hosted on Acast. See acast.com/privacy for more information.
The landscape of industrial machinery and manufacturing has seen an innovative overhaul of technological advancements.
Siemens is one of the largest industrial automation supplier in the world, with a unique position in the software side. They have been a leading provider of industrial automation for a number of years so they understand how technology needs to be integrated into the machinery.
Today, in our first podcast in this series, Bill Davis and I, we're discussing how machinery manufacturers are gaining a competitive edge by implementing smart manufacturing.
Bill Davis is the Director of Industrial Machinery & Heavy Equipment Solutions at Siemens. He has a Mechanical Engineering Degree, Bachelor in Science Degree from Milwaukee School of Engineering, with a Masters in Business Administration from Marquette University. In the course of his experience, he has gained a lot of skills with regards to CAD and PDM, as well as operations management.
Listen to the First Episode of Siemens PLM Podcast series to learn how machine manufacturers are maximizing profits, and the industry trends driving the adoption of this innovative technology.
Questions I ask:
· Within that 30-year span of your career, how long have you been focused on smart manufacturing? (02:28)
· What is smart manufacturing? (03:01)
· In what way is Siemens PLM implementing smart manufacturing into companies and into manufacturers? (06:08)
· In looking at just the trends in this industry, how do you see Siemens with the machine trends and aligning that with smart manufacturing? (08:38)
· How are you seeing trends changing in the way customer purchases a machine? (12:52)
In this episode, you will learn:
· Bill Davis’s background and career. (01:15)
· Smart manufacturing at the product level. (03:55)
· Smart manufacturing at the machinery level. (04:32)
· What adaptability means, in terms of smart manufacturing. (09:42)
· What extendability refers to, in terms of smart manufacturing. (11:22)
Connect with Bill Davis:
· LinkedIn
Hosted on Acast. See acast.com/privacy for more information.
The final episode in the current Smart Manufacturing podcast series covers sustainability, a significant global topic across many industries that minimize adverse effects and takes action to contribute to the business and improve the industry's impact on the environment.
Chris Pennington, Global Industry Marketing Leader for Industrial Machinery at Siemens Digital Industries Software, is joined by Rahul Garg, the Vice President of the Industrial Machinery and Mid-market Program at Siemens Digital Industries Software. They will help us understand how sustainability is becoming a critical across many industries, including manufacturing.
In this episode, you will hear how sustainability in manufacturing includes several factors.
Learn in this episode the following pertinent concepts about sustainability:
The energy to run the production process
The circularity and recycling of the product and machinery to produce it
Recycling of raw materials (bright products) that have value to improve company financials and reduce negative environmental impact
A focus on machine design and energy efficiency
An improvement in supply chain energy consumption and recycling practices to ensure parts are available.
The development of workflows and productivity, supply chain, carbon neutrality, traceability in supply chain and circular economy tracking
Creation of energy-efficient machines with lower operating costs
Leveraging digitalization to optimize energy-efficient systems
Connect with Rahul Garg:
LinkedIn
Connect with Chris Pennington:
LinkedIn
Hosted on Acast. See acast.com/privacy for more information.
In today’s world, quality is an aspect that is of great significance to regulators and consumers. Manufacturers are expected to deliver high-quality products while still offering competitive prices. That, coupled with supply chain issues, puts a lot of pressure on them. One way to ease that burden is by fine-tuning the manufacturing process using smart machines.
Today, the host Chris Pennington, Global Industry Marketing Leader for Industrial Machinery at Siemens Digital Industries Software, is joined by Rahul Garg, the Vice President of the Industrial Machinery and Mid-market Program at Siemens Digital Industries Software. He’ll help us understand what closed-loop quality entails.
In this episode, you’ll learn about the goal of closed-loop quality and the impact it creates. Additionally, you’ll hear about what is required to implement it and the performance change in companies that have implemented it.
What You’ll Learn in this Episode:
The importance of integrating quality into the manufacturing process (01:19).
The goals of closed-loop quality (02:22)
The impact of implementing closed-loop quality (05:15)
How deploying advanced technologies results in improved quality (07:32)
Closed-loop quality in future factories (11:15)
Connect with Rahul Garg:
LinkedIn
Connect with Chris Pennington:
LinkedIn
Hosted on Acast. See acast.com/privacy for more information.
An unstable supply chain and an increase in customers’ need for custom products are some of the biggest challenges that manufacturers are dealing with today. The increased competition means they cannot afford to raise their products because that might result in a loss in market share. That’s why more focus has now been put on lowering the production cost by making the manufacturing process as efficient as possible.
Today, the host Chris Pennington, Global Industry Marketing Leader for Industrial Machinery at Siemens Digital Industries Software, is joined by Rahul Garg, the Vice President of the Industrial Machinery and Mid-market Program at Siemens Digital Industries Software. He’ll help us understand what closed-loop manufacturing (CLM) entails.
In this episode, you’ll learn the steps involved in CLM and the benefits of deploying it on a factory floor. Additionally, you’ll find out the role played by product lifecycle management (PLM) and enterprise resource planning (ERP).
What You’ll Learn in this Episode:
A high-level definition of CLM (01:34)
The steps involved in CLM (03:41)
Roles played by PLM and ERP (04:51)
The benefits of linking the production facility and manufacturing engineering to the supply chain (07:01)
The impact of deploying a CLM solution in a production facility (11:38)
Connect with Rahul Garg:
LinkedIn
Connect with Chris Pennington:
LinkedIn
Hosted on Acast. See acast.com/privacy for more information.
A key benefit of digitalizing the factory floor is the elimination of data silos. It provides an opportunity for companies to derive actionable insights from data they were already generating. Such actionable insights can help businesses perform predictive maintenance as well as improve operational efficiency.
I’m your host, Blake Snodgrass, with Siemens Global Marketing, and today I’m joined by Rahul Garg, Vice President of the Industrial Machinery and Mid-market Program at Siemens Digital Industries Software. He’ll help us understand the different roles played by operation technology and information technology.
In this episode, you’ll learn about the current challenges that manufacturers are facing and what they are doing to overcome them. You’ll also find out how IT and OT convergence enables the creation of a digital twin. Additionally, you’ll hear us talk about what the Siemens Industrial Edge Initiative involves.
What You’ll Learn in this Episode:
The challenges that manufacturers are facing today (01:11)
How manufacturers are addressing their current challenges (02:08)
The relationship between information technology and operation technology (03:37)
The benefits of IT/OT convergence (07:15)
Connect with Rahul Garg:
LinkedIn
Hosted on Acast. See acast.com/privacy for more information.
Today, manufacturers are facing challenges such as unstable supply chains and labor shortages. On top of that, they have to keep up with the complexities brought on by an increased need for customized products. One of the solutions that have been successfully employed to cope with these challenges and maintain competitiveness is the adoption of smart manufacturing.
I’m your host, Conor Peick and I’m joined by Dale Tutt, Vice President of Industry Strategy at Siemens Digital Industries Software. Also joining us is Rahul Garg, Vice President of Industrial Machinery and SMB Industries at Siemens Digital Industries Software. He’ll help us understand the problems that smart manufacturing is solving in the industry.
In this episode, you’ll learn about the impact that digitalization is having on the manufacturing industry. You’ll also hear about the impact that smart manufacturing has on the quality of the product as well as the cost of production. Additionally, you’ll learn about the benefits of using the digital twin on the factory floor.
What You’ll Learn in this Episode:
The major challenges in the industrial machinery manufacturing industry today (01:38)
How manufacturers are leveraging digitalization to improve processes (06:01)
The impact of digitalization on automation (09:39)
The meaning of closed-loop quality (12:47)
What the process of building smart machines involves (16:48)
Connect with Rahul Garg:
LinkedIn
Connect with Dale Tutt:
LinkedIn
Connect with Conor Peick:
LinkedIn
Hosted on Acast. See acast.com/privacy for more information.
Intelligent Performance Engineering has the potential to revolutionize how manufacturing facilities operate. But as with any big change that takes place within the industry, it takes time for the value of new technology to resonate. Digitalization changes everything, but how do we best communicate these benefits to customers?
Throughout the series, we’ve taken this deep dive into Intelligent Performance Engineering to help answer questions and curiosities about this groundbreaking technology. We’ve talked about integrated part design, simulation, the digital twin, and how these are reshaping the traditional process models.
Joining us again today are Rahul Garg, Industry Leader for Siemens Industrial Machinery, and Giulio Camauli, Industry Solutions Manager at Siemens Digital Industries Software. As representatives of the industrial machinery industry, they’ve really helped us understand the Intelligent Performance Engineering Solution, and they’ve outlined the benefits manufacturers stand to gain through its implementation.
In today’s episode, we’ll close out this series by summarizing what makes Intelligence Performance Engineering so valuable to customers. We’ll also talk about how the digital twin eases the process of gathering information, share some insights around closed-loop validation, and discuss the unique ability of the digital twin to quickly respond to customer needs.
What You'll Learn In This Episode:
Why closed-loop validation is important for machine builders and suppliers (1:57)
The complexities of data sharing from the customer perspective (3:49)
The benefits of using a digital twin (5:27)
Why the connection between the simulation model and the machine conditions in real-time is so important (10:07)
The biggest advantages for the machine industry embracing digitalization (15:02)
Why Intelligent Performance Engineering is critical for manufacturers(16:07)
Connect with Rahul Garg:
LinkedIn
Connect with Giulio Camauli:
LinkedIn
Connect with Bill Butcher:
LinkedIn
Hosted on Acast. See acast.com/privacy for more information.
Manufacturing technology is full of moving parts. From design to simulation and ultimately production, physical changes to any part of the process can be costly. How can businesses keep up with those changes in a world where frequent customization has become the new norm?
The answer is simple: integration. When part design and simulation are integrated, designers and engineers can work together seamlessly. Proposed changes in design can be simulated using simple drag and drop tools. This integrated approach has the capacity to streamline a process that would otherwise be inefficient and profoundly cost-prohibitive.
Joining us again today are Rahul Garg, Industry Leader for Siemens Industrial Machinery, and Giulio Camauli, Industry Solutions Manager at Siemens Digital Industries Software. Their expertise as representatives of the industrial machinery industry will help us to better understand the ins and outs of the Intelligent Performance Engineering Solution from Siemens Digital Industries Software.
In today’s episode, we’ll talk about the advantages of integrated part design and simulation, how this is benefitting manufacturers, and where the digital twin fits into the equation. We’ll also share a few examples of how companies are successfully applying these integrated systems in ways that weren’t possible with the traditional process model.
What You'll Learn In This Episode:
The challenges that machine builders are facing where the multiphysics simulation approach comes in handy. (01:43)
Why it’s useful to pre-assess any new design modifications and what it entails. (02:50)
The importance of implementing the integrated design and manufacturing process. (04:22)
Why the digital twin is unique in the context of Intelligence Performance Engineering (06:46)
The benefits the manufacturers can achieve by incorporating integrated design and simulation into their manufacturing process. (08:56)
A real-world example of a company that implemented this integrated design and simulation approach. (10:09)
Connect with Rahul Garg:
LinkedIn
Connect with Giulio Camauli:
LinkedIn
Connect with Bill Butcher:
LinkedIn
Hosted on Acast. See acast.com/privacy for more information.
One of the three differentiators of Siemens Intelligent Performance Engineering Solution was designed specifically to meet a very demanding set of requirements. Today, manufacturers demand products that are lighter, smaller, and more complex than ever before. That calls for evermore advanced software that is able to digest a multitude of information and has the ability to effectively communicate that data so that collaboration remains seamless.
Joining us again today are Rahul Garg, Industry Leader for Siemens Industrial Machinery, and Giulio Camauli, Industry Solutions Manager at Siemens Digital Industries Software. Their expertise as representatives of the industrial machinery industry will help us to better understand the ins and outs of the Intelligent Performance Engineering Solution from Siemens Digital Industries Software.
In this episode, we’re diving deeper into Multiphysics Simulation. We’ll talk about how this technology helps companies design, validate, and manage contemporary manufacturing and assembly operations seamlessly despite such complexity.
Some Questions I Ask:
What exactly is Multiphysics Simulation? (1:45)
What are some benefits of Multiphysics Simulation? (4:57)
How does Multiphysics Simulation help OEMs and their broader supplier network, connect and potentially act smarter? (6:15)
How does Intelligence Performance Engineering leverage Multiphysics Simulation to aid in collaboration? (7:36)
What You’ll Learn in this Episode:
A recap of the three key differentiators in the Intelligent Performance Engineering Solution (0:40)
How machinery is approaching the current validation and analysis practices in the field today (3:06)
How Multiphysics allows the user to collaborate more efficiently (5:40)
An example of a company using this technology and how it benefited their bottom line (8:50)
Connect with Rahul Garg:
LinkedIn
Connect with Giulio Camauli:
LinkedIn
Connect with Bill Butcher:
LinkedIn
Hosted on Acast. See acast.com/privacy for more information.
Digital capabilities are proving increasingly valuable in the world of industrial manufacturing. As manufacturing increases in complexity, digital solutions are proving ever more valuable for companies hoping to outpace the competition. In order to address the needs of customers, we rely on intelligent performance and accurate, information-rich simulations.
My guests today are Rahul Garg, Industry Leader for Siemens Industrial Machinery, and Giulio Camauli, Industry Solutions Manager at Siemens Digital Industries Software. As representatives of the industrial machinery industry, they have an advanced understanding of the Intelligent Performance Engineering solution from Siemens Digital Industries Software.
In this episode, we’ll talk about the growing complexity of manufacturing equipment, and why it’s crucial for industrial OEMs to build more accurate, trustworthy simulations using advanced software capable of meeting the needs of customers.
Some Questions I Ask:
What is Intelligent Performance Engineering, and why is this critical? (1:24)
Can traditional processes support the digital twin approach? (3:35)
Has technology been the biggest catalyst for change in the machinery industry? (5:38)
Why is digitalization so important for machine manufacturers? (9:18)
What You’ll Learn in this Episode:
Why there is growing attention towards Intelligent Performance Engineering (2:10)
How the growing demands of flexibility and complexity are being addressed (7:27)
Why intelligent performance is so important in today's marketplace (10:39)
The importance of closed-loop validation (11:58)
Connect with Rahul Garg:
LinkedIn
Connect with Giulio Camauli:
LinkedIn
Connect with Bill Butcher:
LinkedIn
Hosted on Acast. See acast.com/privacy for more information.
Complexity within manufacturing continues to increase at breakneck speed, and from what we understand about consumer demands, it’s clear that this is the new norm. Rapidly changing trends require equipment that can keep up. The industry needs high-level flexibility so that it’s able to adapt quickly when consumer demands dictate.
Manufacturers in-the-know are relying on digitalization, and additive manufacturing is saving the day in more ways than one. By enabling improvements to product quality and design, and with its ability to create complex geometries, manufacturers are using digital parts production to build stronger and lighter products that are out-innovating and out-producing the competition. It’s become clear that the faster companies adopt this digital technology, the more successful they will be.
Back with us today is Rahul Garg, the industry leader for Siemens industrial machinery industry. We’re also welcoming Ashley Eckhoff to today’s show, he’s a member of the Additive Manufacturing Programme team with Siemens Digital Industry Software.
In this episode, we’re taking a closer look at the advantages of additive manufacturing, both in terms of efficiency and quality of parts. You’ll hear how digital parts production leads to less waste and more efficiency, and how creating a digital twin allows manufacturers to take advantage of the data being collected. Finally, we’ll close out the series by summarizing the biggest advantages for the machinery industry to step into digitalization, and how manufacturers can get started.
In this episode you will learn:
The definition of additive manufacturing and its advantages (2:14)
How additive meets the specific challenges that manufacturers are facing today (3:25)
Understanding digital parts production (5:30)
The purpose of a digital twin (6:29)
Additive success stories (9:28)
The biggest advantages of digitalization for manufacturers (12:43)
3 important ways to take advantage of digitalization(15:19)
Connect with Rahul Garg:
LinkedIn
Connect with Ashley Eckhoff:
LinkedIn
Connect with Bill Butcher:
LinkedIn
Hosted on Acast. See acast.com/privacy for more information.
The complex issues that face manufacturers today are myriad. One of the most intriguing solutions is to implement synchronized parts manufacturing. By adopting a closed-loop manufacturing process, equipment manufacturers can improve their planning by introducing intelligence.
Manufacturers often struggle with facilitating communication and timing between the data and people. As the flow of information becomes increasingly complex, synthesizing all that information becomes a major challenge. If manufacturers don’t embrace synchronized parts manufacturing, problems may arise from the data’s lack of organization.
Today, I welcome back Rahul Garg, the industry leader for Siemens industrial machinery industry. I’m joined as well by Brad Rosenhamer, a portfolio development executive focused on manufacturing operations management for industrial machinery, heavy equipment, and automotive markets.
In this episode, you’ll learn about some challenges facing machine builders, the advantages of synchronized parts manufacturing, and how the digital twin fits into the discussion. Brad also discusses some companies that are successfully implementing synchronized parts manufacturing and we’ll explore why adopting this process is a critical strategy for manufacturers.
In this episode you will learn:
Some common issues plaguing today’s manufacturers (02:26)
Why it's so important to have a synchronized part manufacturing process and some of the risks in not doing so (03:30)
About the digital twin in the context of digital part production and synchronized part manufacturing (04:48)
The benefits for manufacturers that incorporate synchronized part manufacturing (06:38)
Why it’s critical for manufacturers to look at the sum of all manufacturing process (08:17)
Some examples of companies that have integrated a holistic approach into their manufacturing (10:28)
Connect with Rahul Garg:
LinkedIn
Connect with Brad Rosenhamer:
LinkedIn
Connect with Bill Butcher:
LinkedIn
Hosted on Acast. See acast.com/privacy for more information.
In today’s competitive market, increasing pressure is being placed on manufacturers. Tied into that pressure is the need to expedite production and bring products to the market faster than ever before. Meeting those needs while keeping part quality at a premium hasn’t been the easiest package to deliver. That is, until highly-automated CAM changed everything.
Understanding the importance of efficiency in high-level manufacturing, the designers behind CAM sought to create a solution that digitized the design and manufacturing process, while connecting the various types of software from every aspect of the part-making process. It also allows companies to capture and reuse data, minimize waste, and increase overall efficiency. With CAM, manufacturers can now pivot quickly when digital threats arise.
Today, we’re taking an in-depth look at highly automated CAM, or Computer-Aided Manufacturing. Here to help us understand how this technology works are Sashko Kurciski, leader of the marketing efforts for Siemens part manufacturing software portfolio, and Rahul Garg, Industry Leader for Siemens Industrial Machinery.
In this episode, you’ll hear about how CAM links manufacturing, engineering, and production, resulting in better efficiency and simplified communication across the board. Sashko and Rahul will also share a couple of real-world examples of early adopters to CAM, and you’ll hear how manufacturers are differentiating themselves by taking advantage of this technology.
In this episode you will learn:
A breakdown of CAM software and how it helps manufacturers (2:38)
One example of a highly automated CAM solution (4:51)
The shared goal of modern manufacturers (6:58)
Why software connectivity is so important (10:05)
How the digital twin saves time (13:51)
The role of additive manufacturing in part production (16:59)
How digitalization helped a Netherlands-based manufacturer perform better (18:25)
The link between automation and efficiency (20:49)
Connect with Rahul Garg:
LinkedIn
Connect with Sashko Kurciski:
LinkedIn
Connect with Bill Butcher:
LinkedIn
Hosted on Acast. See acast.com/privacy for more information.
Comments
Top Podcasts
The Best New Comedy Podcast Right Now – June 2024The Best News Podcast Right Now – June 2024The Best New Business Podcast Right Now – June 2024The Best New Sports Podcast Right Now – June 2024The Best New True Crime Podcast Right Now – June 2024The Best New Joe Rogan Experience Podcast Right Now – June 20The Best New Dan Bongino Show Podcast Right Now – June 20The Best New Mark Levin Podcast – June 2024