Discover
The HSE Podcast
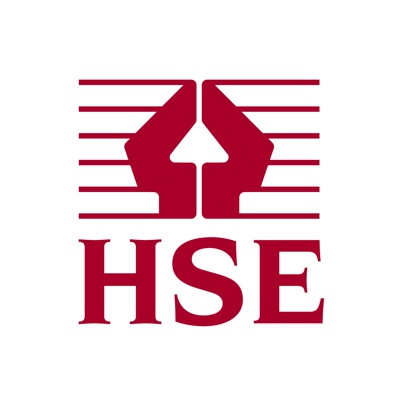
The HSE Podcast
Author: hsepodcast
Subscribed: 67Played: 304Subscribe
Share
© Copyright 2020 All rights reserved.
Description
In 2022, The Health and Safety (HSE) launched a new 10-year strategy: Protecting People and Places. This is strategy that reflects HSE’s role at its broadest. A role that goes beyond worker protection, to include public safety assurance on a range of issues, as we adapt to new technologies in the workplace, the government’s commitment to the net zero agenda, and HSE’s added responsibilities, such as becoming the appointed Building Safety Regulator and our extended role in chemical regulation, post Brexit.
This Health and Safety Executive (HSE) series of free podcasts will cover a range of subject matters to help businesses and workers understand HSE’s strategic priorities, its campaigns and the main challenges we collectively need to address.
After each initial broadcast the podcasts will remain available to listen on demand.
This Health and Safety Executive (HSE) series of free podcasts will cover a range of subject matters to help businesses and workers understand HSE’s strategic priorities, its campaigns and the main challenges we collectively need to address.
After each initial broadcast the podcasts will remain available to listen on demand.
13 Episodes
Reverse
In this podcast, HSE Chair Sarah Newton and Professor Cary Cooper, one the world’s foremost experts on wellbeing, discuss the importance of working in partnership to prevent work-related stress and to promote good mental health.
Amongst other things, the podcast covers HSE’s Working Minds campaign, which aims to ensure psychological risks are treated the same as physical ones, that employers recognise their legal duty to prevent work related stress to support good mental health in the workplace, and that they have the tools they need to do achieve this.
For more information on the campaign visit ‘Working Minds'
PODCAST TRANSCRIPT
Mick Ord (Host): A warm welcome to you whenever and wherever you are listening to this Health and Safety Executive podcast from me, Mick Ord, and our soon-to-be-announced guests. This podcast is the second in a series designed to help you to make your life a little easier, both in work and maybe even spilling over into your personal life, you never know.
The Health and Safety Executive is committed to improving the health and safety of workers in Great Britain. And today we'll be focusing on an issue that affects all industry sectors, work-related stress, and its potential impact on mental health. In 2020/21, more than 800,000 people suffered from work-related stress, depression, or anxiety. The impact on workers and businesses is considerable. A recent report by Deloitte estimates that the total annual cost of poor mental health to employers has increased by 25% since 2019, costing UK employers up to 56 billion pounds a year. 56 billion! Last year, on the 16th of November, HSE launched its Working Minds campaign to encourage, promote, and support good mental health in the workplace and prevent work-related stress. And today we'll talk about the successes of the campaign, what still needs to be done and why this topic is still so important. Joining us today is Sarah Newton, Chair of the Health and Safety Executive. In addition, Sarah is currently a non-executive director of the Royal Cornwall Hospitals NHS Trust. Prior to taking over the chair in 2020, Sarah's experience includes serving as a director for American Express Europe, Age Concern, and the independent academic think tank, the International Longevity Centre. Sarah was also an MP for ten years, and served as a minister in the Department of Work and Pensions, responsible for HSE and Health and Work Unit.
And we're delighted to also have with us Professor Cary Cooper, one of the world's foremost experts on wellbeing, and a 50th anniversary professor of Organisational Psychology and Health at the Manchester Business School. He's the author or editor of over 170 books, has written more than 450 scholarly articles for academic journals, and is a frequent contributor to national newspapers, TV and radio. A big welcome, both.
Sarah. First of all, thanks for joining us for the podcast. Now, your Working Minds campaign has just celebrated its first anniversary, so tell us about why you launched a campaign in the first place and what it's achieved..
Sarah Newton: First of all, thank you so much for inviting me on to your podcast this morning, Mick. You know, let's be honest about this. Any one of us can experience stress. It can affect people in different ways and different times, so it's a very prevalent issue. So why did HSE get involved with dealing with this? Well, it's clearly our mission to prevent work-related ill health, and as you said from those startling statistics in your introduction, many people are experiencing stress in the workplace, and we know it's the number one reason why people will have an absence from work is. So we were looking at a new strategy last year.
We've developed a new strategy, which is protecting people in places and five strategic objectives. One of them clearly to reduce work-related ill health, with a particular focus on stress because it affects so many people. And we chose to launch this campaign because HSE, while we have a huge amount of expertise, we don't have all the answers. And we really wanted to work in partnership with a wide range of organisations who together, we could bring the big difference that we want to see. It's all about working in partnership, collaborating with others, making sure that employers have the knowledge, the tools that they need to really support their workers to prevent work-related stress and ill health.
Mick Ord (Host): As we've heard the figures on people taking absence from work because of work-related stress have really increased over the past couple of years. What are your thoughts about that, Sarah?
Sarah Newton: Well, I think a part of it, or probably a very large part of it, is to do with the fact as a society, we've been far more prepared to talk about mental ill health. There's been a huge amount of really positive work to de stigmatise mental ill health, which of course includes stress and anxiety and depression. And so I think as a result of that, people are more prepared to acknowledge that they're suffering from mental ill health.
Mick Ord (Host): Professor Cooper, I guess that you'd echo everything that Sarah said there about the Working Minds campaign?
Prof. Cary Cooper: Oh yeah, absolutely. I mean, HSE has always been at the forefront looking at stress at work. It was the only country actually, 20 years ago, set up the management standards for stress at work. I was involved in that 20 years ago. And it's gotten worse, a lot of the problems. That was really ahead of its time, but times have changed. We've had a financial crisis since then. We've had a pandemic. We have a cost of living crisis. We're about to enter a recession. This has really become even more significant and more important than ever before. And the HSE, by revising the management standards, by getting involved in this Working Minds campaign is really quite important. And by the way, it's not just the UK. Every developed country has between 50% and 60% of its long-term absence due to stress, anxiety, and depression. It's not just the UK. This is a kind of global problem, particularly in the developed world.
Mick Ord (Host): Sarah, what are the next steps for Working Minds then?
Sarah Newton: So Working Minds is a collaboration. It's a partnership of a number of organisations. We've already doubled the number of organisations we work with. We're so grateful to our partners. So some of our founding partners such as Acas, Ceca, Mind, Mates in Mind. Now we're working with different industry sectors, so working a lot with their representative bodies across a huge range of industries. And a huge benefit to us of that is to draw on their expertise, but also to reach out to their members. You know, big companies will often have HR departments, they'll have investments into all types of health and wellbeing type programs, but small and medium sized companies don't always have those resources available for their staff. So it's very important that we really reach out to every business right across the UK and provide them with some tools that really will make the difference. Most employers will understand that it's their responsibility to think about the physical risks, the physical health concerns that people can have at work, But what they don't often realise is they have an equal responsibility to the psychological wellbeing of their staff. So part of our campaign is to remind employers of those legal responsibilities. They do have a duty to do risk assessments of their employees for both physical and psychological risks to ill health, and then to provide them with the toolkits to enable them to assess the risk and then manage and mitigate the risk. And by working with so many different employers, really drawing on their experience what works in their workplaces. So an element of this is going to be peer-to-peer support. So businesses say in the agricultural sector, they come, share good experiences together on what works for them. That's a very different sector than say the NHS or working in an advanced manufacturing location.
So while the principles are the same, the applications and probably the examples of good practice will be different. And so we'll be wanting to build on the huge success of the first year, have more people become partners, more people become champions, access the materials that are there so that they can take some really practical actions in their workplaces to improve the health and wellbeing of their staff.
Mick Ord (Host): And as you've already said, it's not just big companies with HR departments, is it? It's the small, maybe a company with 20 employees or something like that.
Sarah Newton: You know how right you are. But a vast majority of people in the UK are employed in small and medium size organisations. And actually recent data will show a lot of people are employed in, you know, what might loosely be called the gig economy, or platform workers. And platform workers, may be just part of their employment. Perhaps they've got a job with an employer, but then they actually supplement that income as a platform worker, and those companies are not in day-to-day contact with their employees, with the people that they are working with to actually deliver the services through these platforms. Now they really need to think hard about how they are going to reach out to those employers and make sure that they are undertaking their risk assessments, so to prevent people having physical or mental ill health at work.
Mick Ord (Host): Cary, you wanted to come in there?
Prof. Cary Cooper: Yeah, Sarah's really hit a really important issue. A lot of the bigger companies since the financial crisis of 2008-2015, have really treated stress at work and wellbeing much more seriously, much more strategically. There are now directors of health and wellbeing in many of the big companies and public sector bodies. Indeed, the NHS have. Every hospital in the NHS has a non-executiv
In this podcast, we discuss HSE’s latest construction initiative focusing on the risks of injuries and aches, pain and discomfort in joints, muscles and bones known as musculoskeletal disorders (MSDs).
With 40,000 construction workers reporting that they suffered with MSDs last year, Matt Birtles, Principal Ergonomics and Human Factors Consultant at HSE and Peter Crosland, National Civil Engineering Director at CECA discuss what the industry can do to promote change and protect its workforce.
Amongst other things, the podcast covers HSE’s ‘Your health. Your future’ construction campaign, the impact that these injuries can have on workers and employers legal responsibilities and the sensible control measures that can be introduced regardless of the size of the construction site.
For more information on the campaign visit ‘Your health. Your future'
PODCAST TRANSCRIPT
[00:00:00] Mick Ord (Host): A warm welcome to you whenever you are listening to this Health and Safety Executive podcast from me, Mick Ord, and our soon to be announced guest experts. This podcast will be the first in a series designed to help you to make your life a little easier, both in work and maybe even spilling over into your personal life, you never know.
The health and Safety executive is committed to improving the health and wellbeing of workers in Great Britain. And today we'll be focusing on the construction sector, a key industry that employs more than two million people and includes employers and building workers, contractors and subcontractors, staff and freelancers alike in a range of organisations from sole traders to multinationals.
Last year did the UK alone, 40,000 construction workers suffered from injuries and aches, pain and discomfort in joints, muscles and bones. Such injuries can have a serious impact on their ability to perform tasks, their quality of life, and in some cases their ability to stay in work and earn a living or having to take time off work as well.
Many people suffer from long term pain and discomfort as a result of injuries sustained on building sites. So with such worrying stats in mind, the HSE are embarking on the Work Right construction campaign. This means that HSE inspectors will be performing a thousand inspections at building sites in the UK.
So what will they be expecting from companies? Joining us is Matt Birtles, an ergonomics expert from the HSE Science Division, and a little later we'll be hearing from Peter Crosland, the National Civil Engineering Director at Ceca, the Civil Engineering Contractors Association.
Well, first of all, Matt, thanks for joining us for the podcast. What should companies expect if an inspector does visit their site?
[00:02:18] Matt Birtles: First and foremost, thank you Mick for hosting us and having us on this podcast. When
an inspector comes knocking on site, first and foremost, expect the norm. So they'll be looking at safety as well as health issues. But what's happening during the campaign especially is there'll be an increased focus on particularly the kinds of risk factors associated with musculoskeletal disorders.
So there's been an awful lot of effort ahead of this campaign within, you know, my regulatory colleagues in HSE to train them upon understanding the key risk factors. For musculoskeletal disorders, how to assess them and what kind of controls they might want to see in place. And so when the inspector does come, they'll be looking at the kinds of manual handling activities and maybe some repetitive work that commonly go on in construction sites and looking specifically at ways in which the risks are controlled.
So there may be some of that manual handling activity happening during the inspection, and they'll just observe that and watch how it's done, where potentially improvements could be made. And also looking at the paperwork and the risk management system. If there aren't any manual handling operations happening at the time of the inspection, they're just more likely to ask principal contractors or ask them on site responsible for safety about manual handling, and ask them to show them their risk management systems, any risk assessments they have, any planned risk controls.
Especially at those points where you'd expect increased manual handling. So moving materials around during deliveries, for example, during fitting or moving plant equipment. And so just an increased focus on musculoskeletal disorders in every inspection for the next six weeks or so.
[00:03:57] Mick Ord (Host): And who specifically is the "Your Health, Your Future" campaign aimed at?
[00:04:02] Matt Birtles: The target really is anybody involved in construction. And so while obviously anybody on the site, you're more likely to see colleague inspectors or regulatory colleagues, we'll be looking at those involved in the design and then planning of construction, and procurement, for example, and then certainly those on the managing sites and working on sites and doing the physical tasks on sites.
And it's aimed at larger construction sites or smaller. And so we're going to try and focus on as many sites as we possibly can and as greater variance as possible. But everybody has responsibility for helping to manage MSDS or musculoskeletal disorders.
[00:04:43] Mick Ord (Host): And why the focus now on the manual handling assessment?
[00:04:48] Matt Birtles: Well, manual handling assessment. It's gotten easier over the years with the advent of the HSE tools like the MAC tool or manual handling assessment charts or the RAPP tool risk assessment for pushing and pulling. For, you know, barrows and the like, Manual handling assessment has gotten much easier. And while doing the assessment using the tile method or L23 method, it meant all the methods involved a checklist of looking at all the different risk factors.
It could be quite arduous and not necessarily give you the answers that would lead neatly to potential solutions. Now, with the MAC tool, which is not new, there's nothing new in the MAC tool per se. It's much easier to actually do a quick assessment and wherever identifying manual handling operations. It's very quick and easy now – even using the online version, which is the new element of all this I suppose – to do a quick assessment and understand the key risks and level of risk. And so the barriers have gone for potentially, arguably, long and arduous risk assessments. It's now very straightforward to do a risk assessment, and so it shouldn't be a barrier anymore.
[00:05:54] Mick Ord (Host): And how serious is the problem of injuries sustained in moving and handling construction materials?
[00:05:59] Matt Birtles: Inevitably being who I am, where I'm from, I'm going to say very. But actually the stats do add up. As you mentioned, 40,000 injuries per year on average in the construction sector. But if you compare that to other industries or the rest of all industry, you’ve kind of almost got double the rates of musculoskeletal disorder amongst construction workers.
So, while across industry, we might see roughly speaking about 1/100 workers getting injured with musculoskeletal disorder, in construction, it's around 1/50. So about 54% of ill health for the construction sector is musculoskeletal disorders. So it's far too common. It affects far too many lives.
Then the other way of looking at how serious it is, is what's the impact on individuals and per individual? What happens to that person, and we may cover this a bit later, but it can affect every aspect of life. Of course, as you mentioned it can impact on your ability to actually go to work and earn a living. But also it can impact on your home activity, mucking around with your kids, the enjoyment you might get from normal stuff like going down the pub, going to the cinema, and those sorts of things.
Because of the nature of the discomfort with MSDs, it can actually affect your ability to stand and make that uncomfortable, but also your ability to sit down and make that uncomfortable. So in those sorts of areas, it becomes very serious because it can really deeply impact on people's health and wellbeing, not just in work, but also outside of work.
[00:07:28] Mick Ord (Host): Peter Crosland from Ceca, Peter, have you got some examples of the kind of injuries that workers have sustained and the actual impact it's had on their lives?
[00:07:38] Peter Crosland: Well, yes. Thanks Mick. And I think yes, all too often where you get examples of people who have worked in the industry for a long time and then suddenly become unable to work.
And coincidentally, I was at a meeting this morning up in the northeast where one of the previous site supervisors had worked for 20 years laying curbs. And actually had a back that was quite wrecked and he really was in a quite a difficult place. And I think we just hear that story all too often. So one of the problems has been the latency effect of all these issues coming to the surface, and I have to say that given the nature of our workforce, which is, I think we'll all know that demographics by now, they've been banded around. You know, many times that there are a cohort of people who have carried out those activities and are now suffering really quite badly, and they're having to move jobs. They're having to step down away from the work that they really, you know, they joined the industry to do and they can no longer carry out those functions. And as Matt says, that then starts to spill over into home life and it affects the quality of life of not only the worker, but also the family.
[00:08:57] Mick Ord (Host): And in that particular example that you just quoted from the northeast, is there anything that you can do to help that particular person if they've been manual handling in a certain way for 20 or so years?
[00:09:10] Peter Crosland: This is probably going to sound slightly negative, but I think sometimes we are a little bit reactive in the industry rather than proactive. Unfo
After UK Transition: Working with Chemicals - Episode 1 - PPP
Plant Protection Products (PPP) - Rachel Brown - PPP lead in CRD (Future Readiness) Transition Programme at HSE and Duncan Williams - Lead for Pesticides Post 2020 Transition Project at DEFRA. We discuss what the UKIM bill means for PPP products/applications, the implications for businesses involved in the manufacture, distribution and supply of pesticides and the data businesses will need to supply to HSE.
Visit our website for further information and detailed guidance on the chemical regimes.
*The information in this podcast was correct at time of publication.
Podcast transcript
Good day and a warm welcome to the HSE podcast brought to you by the Health & Safety Executive to guide you through the changes in chemical regulations which are happening as a result of the UK leaving the EU. In this episode we’ll be hearing from our experts about how plant protection products, otherwise known as PPP Regulations, will be changing from the 1st January 2021 once the transition period is over. From that date a new independent pesticides regulatory regime will operate and Great Britain will take responsibility for placing PPP’s on the market in this country.
My name is Mick Ord and before I introduce you to our guests, I’d like to point you in the direction of the HSE website where the information we refer to today can be found. The place to go is www.hse.gov.uk/brexit. And what I’d also urge you to do is to subscribe to our free bulletin service to stay up to date with all the latest news and guidance on pesticides so you have all the relevant information at your fingertips and you can do this via the website.
Rachel Brown is the HSE’s Transition Programme Manager for Pesticides and Duncan Williams is Team Leader for Pesticides at Defra, the Department for Environment, Food and Rural Affairs.
Mick:
Duncan I’ll start with you if I may. What are the main changes that will apply to plant protection products from January 2021 in terms of PPP regulations?
Duncan:
Ok, so at the end of this year the transition period for leaving the EU will end so that means from the 1st January next year we’ll be operating a new independent pesticides regulatory regime in Great Britain by which I mean England, Scotland and Wales. It’s slightly different in Northern Ireland, so we’ll come onto them shortly. So in Great Britain the EU Legislation is essentially carried over into national law. So, all the regulatory requirements of the current EU regime, all the technical standards, are carried over unchanged into our national regime. It will look and feel very similar to the current EU regulations, except we’ll be taking our own decisions rather than being covered by EU decisions.
That means there’ll be some degree of divergence from EU decisions over time for example maybe different decisions at different times or sometimes different decisions and of course any EU decisions which come into force after the end of this year, won’t apply in Great Britain. If they come into force before the end of this year, they will and they will be carried forward. So that’s things like active substance decisions, Maximum Residue Level (MRL) setting and so on.
Mick:
What about businesses operating in Northern Ireland – what’s going to happen to them?
Duncan:
Ok, so under the Northern Ireland Protocol, the EU Plant Protection Product Regulations and also the EU Maximum Residue Level Regulations – they’ll continue to apply directly in Northern Ireland so there’s less change. So in Northern Ireland the position is basically remaining as much as it is now during the transition period. That means EU active substance approval decisions, MRL decisions, they will all continue to apply directly in Northern Ireland. They’ll still have responsibility for product authorisations under that EU Framework and that function will continue to be delivered by HSE for Northern Ireland.
Mick:
How similar will the new GB regulations be to those from the old EU process?
Duncan:
Very similar. The name of the legislation actually remains the same. We’ll still be referring to EU Regulation 1107/2009 as it applies in Great Britain. Some changes have been made to the legislation so that the regulations can operate properly in a national context outside the EU. For example the EU Regulations for various centralised decision making processes and so on built into them which have had to be replaced by national processes but there’s no substantive policy change. All the retained EU law, retained EU law is what we call the legislation we’ll keep in Great Britain afterwards, that’s been put online at legislation.gov.uk and you can see the changes which have been made to it. The regulatory requirements remain the same and the body of EU technical guidance which underpins the legislation that’s used to make decisions, all of that is carried over as well and will continue to be used in Great Britain after the 1st of January so there’s no change in the standards of protection, the big difference is that decisions will be taken by national bodies rather than through EU processes and EU institutions. So that’s HSE, Defra and the Scottish and Welsh Governments working closely together.
HSE remains the national regulator for the whole of the United Kingdom on behalf of the UK Government and the devolved administrations in Scotland, Wales and also Northern Ireland. HSE will continue to do the majority of the work and decision making and we’ll all be working very closely together in a shared governance framework. HSE will continue to accept applications in much the same way they do now.
Mick:
Rachel, how will the application forms be different to those from the old EU process?
Rachel:
So as Duncan says, the name of the legislation actually remains the same, so we are still going to be referring to EU Regulation 1107/2009, as it applies in Great Britain and this means that a lot of our templates and application forms will actually appear to be unchanged. We will continue to accept applications in the same way as we do now, and will still need a registration report in the same format in support of an application and there’ll only be some really minor changes to the application form such as whether an application is relevant for GB or NI and these will be published on our website in time for use after Day 1.
Mick:
Will existing PPP Product authorisation previously granted by the UK still be valid and if so for how long?
Rachel:
Yes, on Day 1, all the existing Plant Protection Product authorisations previously authorised in the UK, they’ll continue to be valid in both GB and NI. We won’t be issuing any new product notices at all. The existing notices and their current expiry dates will all remain unchanged.
Mick:
Will GB continue to issue parallel trade permits from 2021?
Rachel:
We will no longer be able to accept applications for parallel permits into Great Britain. These are an EU measure and we just can’t operate that outside the EU context.
However, we have put in place some transitional measures to allow time for businesses to adjust and can continue to issue parallel trade permits for sale and use in Northern Ireland.
Mick:
How long will current parallel trade permits be valid for?
Rachel:
So for GB, the existing permits which were granted prior to 31st December 2020, they’ll be allowed to continue until 31st December 2022 or they may expire on their existing expiry date if that is an earlier date before December 2022. The withdrawal action will be published for all those existing parallel import permits and we are hoping that will be done in the first part of 2021. This will allow time for stocks to be used up or for any new applications made under national regimes if necessary.
Mick:
Back to you again Duncan. What is the situation with reference to active substance approval – will they continue to be valid until their expiry date?
Duncan:
On Day 1, 1st January 2021, all active substance approvals which are in place will continue to be valid, they’ll be carried forward in Great Britain obviously the EU regime continues to apply in Northern Ireland anyway so no changes there. We’ll have a new statutory register for active substances in Great Britain. This will be clearly published on the HSE’s website and it will show all the active substances which are approved in GB. It will replace the EU’s list of active substances which are in Commission Implementing Regulations if you are familiar with those and the content is the same at Day 1. So all of those active substance approvals are carried forward and with that new national statutory register, basically an active substance has got to be approved and listed on that register for it to be included in any Plant Protected Products for use in GB.
It’s worth noting that we’ve made some transitional provisions so that the old EU regime can link smoothly to the new national one. One of these is that in Great Britain, the expiry dates of active substances where they were due to expire in the EU within 3 years of the end of the transition period.
Those ones will be granted a 3 year extension under the Great Britain regime and this is because applications for renewals have to be made 3 years before the expiry date and obviously if it’s within 3 years of the end of transition, that date will have already passed when the national regime comes into force so the extension is necessary to have an orderly transition to the new regime. So this means active substances which were due to expire in the 3 year period from 1st January 2021 right through to the end of 2023, they will be extended for a further 3 years in Great Britain. Just for reassurance, we can act sooner if we needed to for any reason so for example if there was new important data or scientific evidence about concerns with a particular substance, then there is provision within t
In this podcast, HSE experts discuss the legal obligation to manage asbestos in non-domestic buildings, highlight where asbestos is likely to be found and explain why it is dangerous.
In January 2024, HSE launched the Asbestos – Your Duty campaign, featuring updated web guidance, including new templates and explanatory videos. The steps to the legal duty to manage asbestos in buildings, and the importance of the campaign, are discussed by Tim Beaumont, HM Principal Inspector Health and Safety, Asbestos Cluster Lead and Samantha Lord, Chartered Occupational Hygienist & Principal Specialist Inspector both from HSE.
They are joined by Craig Barker, Group Property FHS & Asbestos Manager at Marks and Spencer. During his 11 years with the company, Craig and his health and safety team have established robust ways of working to manage asbestos containing materials, developed training for employees, and put controls in place to ensure that the duty to manage asbestos is upheld and the processes are followed when any work is carried out on its buildings.
For more information and to download HSE's free asbestos management plan template, visit: https://www.hse.gov.uk/asbestos/duty/index.htm
HSE Podcast - The duty to manage asbestos in buildings transcript
Host (Mick Ord):
Welcome to the HSE podcast, the latest in a series designed to help and support you because whether you are a business owner, a manager, or a worker. Health and safety is for everyone. In this episode we're taking a look at a hazardous material that has been banned in the UK for the past 25 years, but which still claims the lives of about 5, 000 people a year, more than the number of people killed on our roads.
I'm Mick Ord and we're talking about asbestos. What it is, why it still causes so many deaths, how it can be managed properly and efficiently in the workplace, and what you can do to ensure that you or your employees are not exposed to it. This is all part of HSE's campaign, Asbestos - Your Duty. And, as I'm bound to mention a few times today, you can find the relevant information to help you on the Asbestos pages of HSE's website, https://www.hse.gov.uk/asbestos/duty/
With me are three people on the frontline of asbestos awareness from very practical points of view. Tim Beaumont is HSE's Principal Inspector and a Senior Policy Advisor on asbestos. He's been with HSE since 1999 in a variety of operational and policy roles. His main work right now revolves around coordinating the delivery of the recommendations arising from the Work and Pension Select Committee inquiry into HSE's management of asbestos regulation.
Samantha Lord is HSE's Chartered Occupational Hygienist and Principal Specialist Inspector. She's been with HSE for 15 years. But has been working in the area of asbestos for more than 26 years. She plays an integral role in supporting and enabling HSE's asbestos-related inspection programs, as well as their asbestos campaigns. And she also regularly engages with external partners about HSE's work on asbestos.
And we're delighted that Craig Barker from Marks & Spencer has joined us too. Craig has 20 years of experience consulting and advising on asbestos, with the last 10 years in the retail sector for M&S, where he's the Group Property, Fire Health and Safety and Asbestos Manager. Since 2013, M&S has completely overhauled its approach to the management of asbestos-containing materials. Sixty per cent of the estate was built before the year 2000, meaning asbestos must be considered as a potential hazard. Craig and his health and safety team have established robust ways of working, developed training programs for employees, and put controls in place for any work carried out on the building's fabrics to ensure that the duty to manage asbestos is upheld, and the correct processes are followed. Craig will talk us through their approach to managing the risks of asbestos across their estate.
Welcome all.
Tim, can you explain in layman's terms what asbestos is? And how it causes so many deaths.
[00:03:38]
Tim Beaumont:
Well, thanks, Mick. That's a really important question. Asbestos is a naturally occurring mineral.
When we say asbestos, actually there are a number of different types of asbestos. They're all found in the ground naturally and over many years we've been removing it. It has a number of different qualities that make it rather useful. First of all, it's cheap, it's widely distributed across the globe and easy to get to.
Secondly, it's a really good fire retardant. Thirdly, it's a really good insulating material. So, for those three reasons, it has been used widely in construction, particularly over the last 150 years or so, but most of all, the second half of the 20th century. It's got these wonderful attributes that meant that it was cert to be used in a huge range of structures and properties to insulate and to prevent the spread of fire.
The final thing about it, it's really easy to manipulate. You can weave it, you can turn it into a kind of cement, you can add it to other things, you can put it into other products that you're making. All of these things make it an incredibly attractive and useful material. The massive, massive downside. It, um, forms tiny, tiny little shards, little fibres that are really easy to breathe in.
They go right into the very depths of your lungs, and that's the point where it causes ill health. These tiny little shards, these tiny little fibres, so small that you need incredibly strong microscopes to see, end up causing cancers, lung cancer, but particularly an unusual cancer called mesothelioma.
And it's this cancer that is absolutely linked to asbestos exposure. So, really useful, but also really deadly.
[00:05:34]
Host (Mick Ord):
And mesothelioma, I believe that causes two and a half thousand deaths a year in the UK. I mean, that's astonishing, isn't it?
[00:05:42]
Tim Beaumont:
That is a very high number. It's one of the highest causes of death, particularly in men.
The thing about mesothelioma and lung cancer caused by asbestos is the time delay between being exposed and actually developing the cancer. It can be a number of decades, around about 40 years or so, between being exposed to the asbestos and developing the cancer.
[00:06:06]
Host (Mick Ord):
Tim, is there a safe level of asbestos exposure?
[00:06:11]
Tim Beaumont:
Well, what we're not able to say, we're not able to establish a line In exposure above which you're going to be exposed and it's going to harm your health and below which you're going to be safe That just doesn't exist for asbestos because of the nature of its fibrous exposure type What we are trying to do is ensure that Any material that contains asbestos does not give rise to fibres, and that's the crucial thing with asbestos, the breathable fibres that you might be exposed to.
So that's the focus of our attention when it comes to asbestos management.
[00:06:46]
Host (Mick Ord):
Also, Tim, what buildings may contain asbestos and where can it be found?
[00:06:51]
Tim Beaumont:
Asbestos can be found in any building that's been built, particularly in the 20th century, leading up to 1999, when it was banned from use in construction.
But particularly the period from 1920s, 1930s, up to the mid-80s, you're most likely to find asbestos. And it can be found in literally any building or structure that was built in that time period. So, offices, Schools, hospitals, shops, warehouses and homes may all contain asbestos in different ways. Now on our website, we've got an excellent little picture of a property that shows you where you might find asbestos within that property.
But I just want to be clear, for the benefit of this conversation we're having, we're talking about non-domestic setting. That's because there's a very specific set of legislation and standards in place to for working with asbestos in the non-domestic setting. So, everything you're going to be hearing us talk about today, we're thinking about workplaces in particular.
And that is the focus of the work of the Health and Safety Executive. We want to make sure that in workplaces, exposure to asbestos is properly controlled so that when you go to work, you are not going to be exposed to asbestos fibres.
[00:08:05]
Host (Mick Ord):
Sam, what are the steps to managing asbestos properly? What advice say would you give to a new duty holder operating in an older building?
[00:08:13]
Samantha Lord:
Essentially, if you've got an older building, the first thing you need to do is establish if asbestos could be present. Then what you've got to do is identify the risk from that asbestos. And the reason why I say that is that all the asbestos materials don't have the same risk. So as Tim sort of alluded to, there's a range of different products, but their risk is to do with their inherent properties.
Some materials are quite what we call friable, and they easily release fibres if they're disturbed, or if they actually deteriorate over time. But some are much sort of hard-wearing, such as floor tiles. And you're really going to struggle to get fibre released from those. So, it's important to understand the difference in risk associated with different products.
The other thing that's going to affect the risk is how people processes, maintenance and cleaning sort of happens within that building. So, all the activities that potentially could what we call disturb the asbestos. Because once you disturb asbestos, that is where you'll break down the material and release those fibres.
So, once you've identified the risk, then you've got to manage those risks to make sure no one is exposed. And that's really what we're all here to do. What's Duty to Manage is essentially for. So, I've started off just introducing almost the objective of what Duty to Manage is. But what we've got on our website is a series of steps which actually offer sort of the practical advice which you can follow.
And I can explore those if you
In this podcast, we discuss HSE’s Dust Kills construction campaign. Duncan Smith, Acting Head of Unit, Field Operations Division Health Unit at HSE and Abigail Bainbridge, Group Health, Safety & Environment, Director at Persimmon Homes, and Home Builders Federation H&S committee member, talk us through the risks of breathing in construction dust and what those working in construction need to know to ensure their respiratory health is protected at work. For more information on the Dust Kills campaign, and to download our free resources for employers and workers, visit: Construction Dust - Work Right to keep Britain safe
Dust Kills construction campaign podcast transcript:
Mick Ord (Host):
Every year in the construction industry, there are thousands of preventable cases of irreversible lung disease due to past exposure to dust at work. These diseases often have a life-changing impact and can result in an early death. Indeed, it's estimated that more than 500 construction workers die from exposure to silica dust every year.
And as we'll discover in this podcast, the amounts needed to cause this damage are not large. My name's Mick Ord, and welcome to the latest episode in our series of HSE podcasts designed to make us all better informed about health and safety at work, whether you are a business owner or a worker. So, whether you are part of a large, well-established company, a small business, or a new start-up, we hope you might learn some more about the dangers of exposure to construction dust and what you can do to reduce risk and perhaps most important of all to act now.
HSE inspectors will be visiting construction sites all over the country, checking that employers and workers know the risks involved in breathing in dust, and have the right plans in place, and are using the right controls to reduce the health risks of inhaling construction dusts, including silica and wood dust.
The inspections are being backed up by HSE's 'Dust Kills' campaign which offers accessible advice and guidance on the Work Right website, which we'll be mentioning again later, and putting a link in the episode notes accompanying this podcast.
With me are two people who will be able to tell us some more about the health risks of inhaling dust in places such as building sites and workshops, and crucially, what can be done to significantly reduce those risks. HSE's Duncan Smith is a chartered occupational hygienist with more than 30 years of experience.
Duncan was a consultant in the private sector before joining HSE as a specialist inspector in 2010. He's currently the acting head of operations in the Field Operations Division Health Unit.
Abigail Bainbridge is the Group Health and Safety and Environment Director at one of the country's largest house builders Persimmon Homes. She's also a member of the Home Builders Federation and has a background in health and safety law. Welcome both.
Duncan, if I can start with you first, how big is the problem of occupational lung disease in the UK?
Duncan Smith:
Thanks, Mick. Across all industry sectors, there's an estimated 12,000 deaths each year due to previous exposures at work. This is a key priority for HSE to reduce work-related ill health. Of those 12,000 deaths, there's approximately 500 construction deaths each year due to past exposure to silica alone.
Mick Ord (Host): Those are really worrying numbers, aren't they? So, what specifically is HSE doing about this?
Duncan Smith: As I said, this is a key priority for HSE, and every year we're actively inspecting the construction sector. We will go out and have health initiatives, and we have data for 2022 where there were two major health-focused initiatives including this particular respiratory health initiative.
HSE inspectors did something like 1,268 inspections during the respiratory health initiative, and the topic of control of silica exposure was considered by inspectors 512 times. They found that the best standards were seen at home build sites and the worst practices were at domestic refurbishment and street works inspections.
And then thinking specifically about respiratory sensitisers, this is where wood dust exposure is important. Respiratory sensitisers, where the substance may cause occupational asthma. Inspectors considered this particular topic 347 times, and again, poorer standards were noted compared to during previous initiatives, and domestic refurbishment was where the highest non-compliance was seen.
Mick Ord (Host): What are the key things that construction workers need to know then Duncan?
Duncan Smith: It is important that construction workers understand the hazards that they're working with. HSE has some very good information on their website, and the Dust Kills campaign gives a lot of really good information about this.
Thinking about the hazards in construction, silica dust is very frequently experienced. Even though silica is a naturally occurring substance, it is a hazardous substance when used at work, and we may not always be aware that we are using silica because it might be present in some construction materials such as brick or mortar or cement or paving slabs or tiles.
The dust can be very fine when power tools are used, and it can get very dusty. If that very fine dust is breathed down deep into the lungs it can cause serious lung diseases such as lung cancer or silicosis or something called chronic obstructive pulmonary disease (COPD). These diseases are often irreversible and can cause permanent disability and early death.
The risk is often from exposure over a long period. You may not always notice symptoms for a long time, but each exposure to that dust adds up within the lungs and the airways can get progressively more and more damaged. Unfortunately, by the time you do notice you have a problem, the damage is done. The disease can also be made worse by smoking.
Silica is only a risk once it forms fine respirable dust. And by that we mean when it's so small, it can get down into the deep lung. The greater the level of dust in air, the higher the risk. High dust levels are caused by some of the following factors. High dust concentrations. Now, these could be caused by the use of power tools because of the motive, force, and power that they have in them generate lots and lots of dust.
For example, cut off saws, or power saws, grinders, wall chasers, and grip blasters. These can produce very high amounts of dust in air in a very short time. Similarly, dry sweeping using a sweeping brush can make lots of dust or raise lots of dust when compared to vacuuming or wet brushing. The location might be an important factor as well.
The more enclosed the space, the more the dust can build up, and it may not be diluted as it might be if it was outside. The longer the time dust is generated over, the more dust there will be, and if you spend a lot of time in that environment, the more dust you could potentially breathe into your deep lung.
And frequency as well. The more regular the exposure occurs, such as day after day, this increases the risk quite a lot. So, what you do need to do to protect yourself is to follow the hierarchy of control that is set out in the COSHH regulations –the control of substances hazardous to health– at a very high level.
That starts off at: can you eliminate the risk from the process? So, can you eliminate dust by effective design and planning of the process? If you can't do that, then you're going to need to minimise the risk by using suitable control measures. you should always ensure control measures identified are used properly, and that's going to require training and supervision of those that are using the control measures.
Mick Ord (Host): Thanks, Duncan. Abigail Bainbridge from Persimmon Homes within your company and through the Home Builders Federation network of businesses, what's being done to protect workers' respiratory health on site?
Abigail Bainbridge: Thanks, Mick. Well, it's certainly in terms of persimmon and my home builder peers, we are really looking at a simple set of controls.
Firstly, we try where we can to eliminate the risk that can be getting the manufacturer to pre-cut materials, for example, bricks or wood. We also want to make sure we're using the right tool or method for the job. For example, using a block splitter rather than a saw to cut blocks, so it reduces the amount of dust that's created.
We also use, uh, water suppression to dampen down the dust, and even now you can get battery-powered dust suppressors. We also make sure that the right kind of vacuum is being used. We don't want those Henry Hoovers out there; we want a proper M-Class vacuum being used when cleaning up. One of the biggies for all of us is the use of FFP3 masks and ensuring that the user has been face fit tested and is clean shaven.
We all know that using an FFP3 mask whilst the person's wearing a beard or has stubble, is a bit like a scaffolder wearing a harness without clipping on. So that's one of the big areas that we all try and enforce. We also like to use local exhaust ventilation on certain equipment like chop saws, routers, and sanders.
So, Yeah, a multitude of measures, but all, all relatively simple ones that the large home builders like Persimmon can use, but also the smaller SMEs as well.
Mick Ord (Host): You mentioned, uh, face masks there and I was fascinated when I looked at the HSE website one of the information sheets to see that people with stubble and beards really shouldn't be allowed to wear certain types of masks.
Abigail Bainbridge: Absolutely. Yeah, and it's a big problem for us, and I think across the whole industry as well. I think beards are quite trendy at the moment as well, which makes it difficult for us, especially when managing our contractors. So yeah, I think that's one of the biggest challenges for all of us, is trying to educate our contract workforce that just having a
In this podcast, we discuss HSE’s simple principles and guidance to support disabled workers and workers with long term health conditions in the workplace.
Moya Woolley, Occupational Health Policy Team Leader at HSE and Rebecca Hyrslova, Policy Advisor at Federation of Small Businesses (FSB) discuss the guidance and Talking Toolkit to help businesses create an inclusive approach to workplace health.
For more information on the campaign visit Work Right for everyone - Work Right to keep Britain safe
HiEB Podcast: Disability in the Workplace Transcript
Mick Ord (Host):
A warm welcome to you wherever and whenever you are listening to this HSE podcast on disability in the workplace. My name's Mick Ord, and over the next 30 minutes or so, we'll be looking into how businesses can support their disabled staff. And along the way, dispel some of the myths and assumptions that are knocking around about the rights of people with disabilities at work, including those with long-term health conditions.
According to the Federation of Small Businesses, 25% of company owners are either disabled or have a health condition. And given that there are 5.5 million small businesses in the UK, that percentage amounts to more than 1.3 million disabled-owned companies. That's before you even begin to count the number of disabled people in work.
In 2022, there were 4.5 million disabled people in employment according to the Department of Work and Pensions. And yet there is still a perception among many people with disabilities that companies could still do more to understand and support them in the workplace, even though they've undoubtedly been great strides over the past 20 or 30 years.
Last November, HSE published a new guidance for businesses, which they called the Talking Toolkit. It's a really practical guide, which stresses the importance of making sure workplaces are accessible for disabled people and that staff communication is clear and inclusive with the appropriate occupational health support available.
Moya Woolley is Occupational Health Policy Team Leader at HSE, and one of her priorities is to manage the delivery of this new guidance to benefit workers and managers. Moya, welcome to the podcast.
Moya Woolley:
Hello.
Mick Ord (Host):
Nice to see you.
Rebecca Hyrslova is a policy advisor at the Federation of Small Businesses and is the FSBs lead on their disability and health policy portfolio.
Last year, the FSB published a report Business Without Barriers, identifying the issues which affect business owners and highlighting what actions we can take to make our businesses successful for everyone involved, Rebecca, thanks for joining us in the podcast.
Rebecca Hyrslova:
Hi, Mick, great to be here today.
Mick Ord (Host):
Now, Moya, if, if I can start with you, why did HSE feel it necessary to produce the toolkit in the first place?
Moya Woolley:
Great question. So, the guidance we developed was in response to a government consultation that is called Health is Everyone's Business. And it also fits really nicely with HSE'S 10-year strategy to reduce work-related ill health. The Government's response to the Health is Everyone's Business consultation, which we also call HiEB, was published in July 2021. And set out some of the measures that government will take to protect and maintain progress made to reduce ill health related job loss and provide better workplace support for disabled people and those with long-term health conditions.
The measures that government have taken forward include providing greater clarity around employer and employee rights and responsibilities. Addressing the need for employers to have access to clear and compelling information and advice that is easy to understand and is trustworthy and accessible. And also to encourage more employers to provide access to expert support services such as occupational health.
At HSE, we know it's not always easy to recruit people that you need to help your business thrive, which is why it's so important to keep and develop talent in your business. And as part of that, we developed this in non-statutory guidance. It strengthens existing guidance and provides seven clear and simple principles that employees are expected to apply to support safer people and those with long-term health conditions in the work environment.
The seven principles guide you through how best to create a supportive workplace and focus on the key elements to do this, including how you can develop your worker skills and communicate in an accessible manner. Our HSE guidance is just part of government's response. Our colleagues in DWP and Department of Health and Social Care Joint Work and Health Unit have designed a new digital information advice service to help employers and small and medium sized enterprises to support and manage disability and health conditions at work.
This is a dynamic service, which provides a tailored journey for employer users and provides a high-level overview of information and signposting onto trusted resources for service support, such as HSE's new principles, and Talking Toolkits. The new digital service from the joint unit and HSE's non-statutory principle-based guidance are designed to work together and feel seamless. They provide additional support to employers on managing health at work with different formats available to be accessible for all employers, irrespective of size or digital capacity.
Mick Ord (Host):
Now, is it fair to say that the toolkit is designed to ensure that more disabled people gain employment and set up their own businesses and also that those in employment are retained in the workplace and don't leave because they may not be getting enough support at work?
Moya Woolley:
Yep. I think that's fair to say. At HSE, we considered a range of ways that you as an employer can support a disabled worker or a worker with a long-term health condition in the workplace. It's hoped the guidance may help prevent disabled workers or those with long-term health conditions falling out of work. It will help workers feel supported, valued and hopefully lead to happier, more productive work environments. The guidance may also help businesses retain key talent, which can save the resource and expense of recruiting. Advertising, interviewing, onboarding, and training new staff cost businesses significant amounts of money that can be saved if businesses can support their workers adequately and help them thrive and remain in roles.
We base the seven principles of a non-statutory guidance on the Prevent, Promote, Support model, which aims to protect people in work and keep them healthy and productive. Promote to build their knowledge and understanding and transparency within workplaces, considering the health of the workforce and how that interacts with work and to support to help people get back into work and remain in work.
We also develop the principles with disability charities, unions and business representatives in a task and finish group. So, we know that the principles work to those we want to apply them. The principles represent best practice and go beyond what the law requires, though following them will help you develop a supportive enabling workplace culture. And many of the principles require only small changes to be made, which can have a huge impact on an individual's experience at work.
Mick Ord (Host):
Now Rebecca, I mentioned the FSB report, which was published last year: Business Without Barriers. What would you say are the main barriers to more employment of disabled people, either running their own businesses or as employees?
Rebecca Hyrslova:
Thanks Mick. Also, thanks to Moya. It was great to hear a little bit of the HSE's perspective on the toolkits that we also were a part of creating. To answer your question, Mick, you ask about disabled employees and disabled business owners, and I think there's a great overlap in the barriers that they experience, perhaps from slightly different angles.
So, in our report, Business Without Barriers that you mentioned, we found that 52% of disabled entrepreneurs have experienced some form of barrier due to their disability or health condition, and the three that were most commonly cited: 34% said that they were unable to commit consistent hours or meet very short deadlines. Then we had 15% of disabled entrepreneurs struggling to get or apply for even financial support. And then 11% cited access to equipment as a barrier. There were some other issues often around business support and accessible training. Now, I appreciate that it's not going to be every disabled employee's everyday battle to apply for finance, but that sort of issue around very strict deadlines or perhaps, you know, written applications, a strict format that may not suit them. That can be said for disabled employees as well.
So, the barriers are around perhaps flexibility, whether that is to do with work pattern or even the format of the actual job that they have to carry out or even the application process. So that's the sort of retention and recruitment issue. I actually spoke to one of our members who is a disabled business owner and because of his disability, he has this key focus in his work to get more disabled people in the workforce.
He told me a little bit about how he tries to tackle these barriers that he had to overcome himself to enter into the workforce, but also to get more people into his business. And he talked about how he recently hired a web developer, and it was through a standard hiring process, and the employee did not disclose any disability at that point.
So, it wasn't until he was sort of well into his job that it became obvious that he's not really great when it comes to long conversations. So long meetings, generally group conversations, and also client interaction, direct client interaction. So, because he's aware just how important open communication is, he made sure that that's established in his business.
And t
In this podcast, we discuss HSE’s agriculture campaign Your Farm Your Future, focusing on the risks of transport on farms with moving vehicles being are the highest cause of deaths in British farming.
Adrian Hodkinson, Agriculture Sector Lead, at HSE and Brian Rees, Farmer and Safety Trainer discuss some of the most common issues and what farmers can do to make small changes to protect them, their families and workers.
For more information on the campaign visit Work Right Agriculture - Work Right to keep Britain safe
PODCAST TRANSCRIPT
Mick Ord (Host): If I were to ask you which sector of British industry was responsible for the highest rate of deaths and injuries per 100,000 workers, what would your answer? May the construction sector? No, it's the agriculture sector. My name's Mick Ord, and I'm here today on this HSE podcast to introduce you to some guest experts on the subject of safety in the agriculture sector.
HSE has just launched its Work Right Agriculture campaign to encourage everyone who works on the farm to take a little time out and think about how they could improve safety. My word is it needed. Over the past five years, there have been 161 fatal incidents on our farms and 11,000, yes, 11,000 injuries each year. We want to make 2023 a much safer year on our farms, and you can play your part by really engaging with the campaign, looking closely at the way in which you work, and thinking about how you can make it safer for everyone. Joining me today are two people who'll be able to help you to do that.
Adrian Hodgkinson is the head of HSE'S Agriculture sector and a Principal Inspector. He has many years’ experience and works with all the main agricultural organisations to improve the lives of everyone on farming. Adrian, welcome to the podcast.
Adrian Hodkinson: Good afternoon, Mick. Really good to be speaking with you.
Mick Ord (Host): And Brian Rees is a farmer in mid Wales and has been a safety instructor for nearly 40 years. Brian keeps sheep and hens on his farm and is involved in the Wales Farm Safety Partnership. Hi Brian.
Brian Rees: Hello. Nice to be here.
Mick Ord (Host): Adrian, can I start with you? Can we get down to the specifics straightaway? HSE has launched the Work Right Agriculture campaign to try to get those worrying stats down.
Do you know what the main causes appear to be?
Adrian Hodkinson: In agriculture workplace transport and moving vehicles are the biggest cause of fatal accidents in farming, people being killed in farming. And they account for a huge amount of the major injuries that we also see.
Mick Ord (Host): As you say, you've split the campaign into three main sections. Talk to us, if you will, about the first bit: Safe Farms. What areas are you targeting here?
Adrian Hodkinson: When we are talking about safe vehicle movements, we're talking about three things, really. It's the Safe Farm, having a Safe Environment, having a Safe Driver, and also a Safe Vehicle. So, in relation to having a safe farm, it's really about the layout of the farm, thinking about how you're segregating people from machinery.
Really, really crucial to keep people – pedestrians – away from moving machines. It's a good idea to maybe have a marked route where you've got frequent crossings across a yard, put up barriers or posts when you're opening a barn door and walking out into the yard just to make you stop and think and look around for vehicles, putting up signs, warning people that this is where people are going to be walking.
Having mirrors on the corners of building so you can see round and see what's coming. Maybe improving the lighting. Lighting's got a lot better nowadays with LED and all the rest of it, and you can really improve the lighting really effectively on farms and, um, making sure people are visible. At night, or when it's getting dusky, make sure you're wearing that high visibility clothing so you can be seen by drivers coming onto the farm or into the farm yard.
Mick Ord (Host): And that's true in the mornings as well. A lot of farmers starting very early , and it's quite often very dark in the mornings. It still is now, isn't it?
Adrian Hodkinson: Absolutely, Mick. Yeah. Well, when I say the evenings, I mean anytime when it's getting dusky and dark or just starting to be light in the mornings. So important to have good lighting, um, and make sure people can be seen.
Mick Ord (Host): Now you mentioned signage there and that's one of the things when I've been on farms, sometimes something will just appear around the corner, won't it? You know? So, I guess you would say the more signage, the better?
Adrian Hodkinson: Well, you don't want to go overboard, but having signs up just before, before you're approaching a busy area where people might be near the farmhouse or where children might be present, just to slow the driver down and think about what might be just around that corner, just putting up where it's needed. It really makes a difference.
Mick Ord (Host): Now, as a Principal Inspector, you've obviously visited farms of all sizes over the years. Generally, what would you say is the standard, like in terms of safe farms?
Adrian Hodkinson: Well, all farms are different. They do a fantastic job bringing in the food this country needs. We see a wide variety of different standards, so we, we see the huge farms that are really big commercial enterprises, and you get really good traffic arrangements in those sorts of places.
And then you get the smaller farm might be one man and his wife and small family running a smaller farm. And the standards can be equally as good, but they're much simpler usually. But it's so important to make sure that when people are coming on with deliveries, when vehicles are moving around in a hurry, at silaging time or at harvest time, that um, people are kept away from all that moving activity.
Mick Ord (Host): And you've got lots of walkers and hikers, haven't you? Everywhere. And it's quite easy, and I've done it myself to wander onto a bit of land that's private land, not knowing it necessarily, and all of a sudden you're on a private farm.
Adrian Hodkinson: Yeah, and we're coming up to Easter holidays, so it's a really good point, Mick. We're coming up to Easter holidays. There'll be a lot more people out enjoying the, the great British countryside. There will be more people around. Um, some parts of the country are much busier than others. If you're in the Peak District or in South Wales, uh, in the Brecon Beacons or wherever it might be, there's going to be lots and lots of people around at that time of year. So, looking after members of the public and keeping them away from moving vehicles is a really, really good point.
Mick Ord (Host): Now, Brian Rees, as I mentioned before, in addition to running your own farm and being a safety inspector for 40 years or so, you're also involved in the Wales Farms Safety Partnership. Have you got a real life example from one of the farms that you visited where there's been an accident as a result of poor safety procedure?
Brian Rees: I could keep you going for two hours on these. Yeah, it's amazing. You may go into a farm to do some training and you, if it's a lift truck course, you're usually there a couple of days and some take it very seriously and some almost consider it, you know, proud of it. I know one friend of mine, a family who know very well, the son rolled a quad on an open hill and it rolled for about 150 meters and smashed up down by the side of the main road. That really sort of, uh, gets to me a little bit, a lot of accidents on farms and there's a variety of reasons really. Farmers are rushing around. When a farmer needs something that needs doing, they only have one thing on their mind, and that's to get that job done and they don't necessarily think of what's happening around them.
A very good friend of mine, two years to now, he was calving. And one morning he went into his shed, the cow had calved, and there she was in the pen. They were lambing as well. So, they were busy doing other things. He went back by this cow in about an hour's time. The calf was looking a little bit hollow and he thought it hadn't sucked.
So he gets his wife when they get a jug of water, and you know when a calf hasn't sucked you have to put a tube down his throat into his stomach to get him going. So, he went into the cow, and she was fine. He actually milked about a couple of litres of colostrum off the cow, and he just turned his back on the cow and he caught hold of the calf and he was just opening his mouth, and the calf makes a little, "urrrghh" sort of sound and this cow just went berserk! Now his wife was facing the cow. She could see what happened. So, she tried to throw the jug of milk that she was holding at the cow, and she managed to escape. But Rob got really, she really mangled him. Now then, he's still alive, and I keep telling him regularly, he's very lucky to be alive. The son appeared from somewhere fairly quickly and he's a fairly big lad, and he literally manhandled this cow off him. It was amazing. Now, Rob used to be six foot two, he's now six foot and half an inch, because it smashed one complete vertebrae out of his back and they pinned him all back together. He's okay. But uh, you speak to him on a cold morning and he can hardly move, you know.
And that's just an example where it could have been cured so simply, you know, We actually filmed Rob on the farm and although his system was in place really, he had really quite good calving pens, the secret is you never get between the calf and the cow. Whatever you're doing, you've got to always be behind the barrier. Little things like that. But all that was on Rob's mind at that time, was getting milk into that cow's belly. Everything else goes out the window, and I think that happens with a lot of farm accidents.
Another one not far from here in North Wales, where a chap pulled a tractor on a steep slope. Top quality farmer, you k
After UK Transition: Working with Chemicals - Episode - 6 - Questions and Answers session
The latest episode of HSE’s Working with Chemicals podcast series invites industry voices to answer questions from organisations relating to the GB chemicals regulations.
Whatever branch of chemicals industry you work in, we offer advice and guidance to support your business and point you in the right direction.
Visit our website for further information and detailed guidance on the chemical regimes.
https://www.hse.gov.uk/brexit/chemicals-brexit-guidance.htm
PODCAST TRANSCRIPT
Good day and welcome to Episode 6 of the HSE podcast with me, Mick Ord.
For today’s podcast we’ve got a line-up of guests whom regular listeners will recognise from previous episodes and we’ll also be hearing from a special guest who hasn’t appeared before – he’s the Director of the Chemicals Regulation Division of HSE, Richard Daniels.
What we thought we’d do in this episode is go through each regime with the relevant experts and pick out some of the big themes and questions which have emerged from our discussions with companies since the transition period ended last year.
So many of you have been logging onto the HSE website and getting in touch with us as Richard will explain a bit later and we thank you for that – please continue to do so.
So whichever branch of the chemicals industry you work in, if you have questions relating to the GB chemicals regulations, we hope we can cover it here and reassure you that a) you’re not alone and b) we are doing and will continue to do everything in our power to point you in the right direction.
So without further ado – the regimes we cover in this episode include Biocides, Pesticides, CLP – that’s Classification, Labelling and Packaging of chemicals, and REACH – that’s the Registration, Evaluation, Authorisation and Restriction of Chemicals.
Our first expert today, Dr. Nicola Gregg, is Team Leader for Biocides Operational Policy in HSE’s Chemicals Regulation Division.
Mick:
Hi Nicola, first query for you. I’m a small business that produces coatings and I have an application for a biocide product that I wish to register under Great Britain Biocides Product Regulation (BPR), what format do I need to submit an application in?
Nicola:
First of all, it’s worth pointing out that as HSE no longer has access to R4BP, the EU systems, they will need to submit their application directly to us in HSE using our new forms and these forms are available for download from our website. So they download the form, complete all the details and email them back into us and when we receive the form, we then send out a secure upload link and it’s into that that they submit all your data and information. Don’t send the information and data in an email, wait for the secure link. So the sort of information which we would expect to see uploaded would be for example the Active Substance Competent Authority Report (CAR), the Product Authorisation Report (PAR), Summary of Product Characteristics (SPC) all terms which people will be familiar with as well as all the supporting data. Now for all those reports that I just listed there, we’ve got new templates for these as well on our website. We’d very much like applicants to use these new templates, unless they’ve already got the information in the EU versions of those templates. So in other words, if they’ve already got it in the EU version, we don’t expect them to repeat the process and fill out our templates. For new applications, please do use our new templates.
We also expect that they submit their data in IUCLID - we would prefer IUCLID 6. If they have got data in older IUCLID versions, submit them and we’ll see if we can access them and obviously if we can’t then we’ll get in touch and we’ll work out how to move forward.
Now we do realise that some of the data that was submitted a long time ago might never have been in IUCLID and that’s OK for resubmissions that we’ve talked about previously, but probably if we receive an application from an applicant and see no IUCLID, our automatic response almost will be – where is your IUCLID file so you just need to explain that you never had a IUCLID file in the first place.
There’s one final thing Mick that I’d just like to highlight as well – that we do need active and product reference lists. So these reference lists for both the active and the product applications must be on the GB Excel template – that’s one area where we aren’t able to be flexible.
Mick:
OK, another question. I produce wood preservative products and wish to have my product on the market in the GB and NI. What do I need to do?
Nicola:
Well, applications for Northern Ireland, just like the GB applications, will be made directly to HSE using our new forms as I’ve just described and using the same submission methods. There is one exception however. That exception is if a company wants to apply for an EU Union authorisation so that would include Northern Ireland, and Union authorisations, these applications follow entirely the EU system so the applications are made using R4BP. HSE will have no involvement in the processing of Union applications.
We are still discussing some details with ECHA about mutual recognitions and we can confirm that if a company applies to the EU and wants the product to be mutually recognised into Northern Ireland, they can do that via what we call Mutual Recognition in sequence process. Now it’s not yet quite clear whether they can apply for Mutual Recognition in parallel into Northern Ireland and when we have a clearer picture on that, we will be able to confirm one way or another. But mutual recognitions for Northern Ireland again are submitted directly to HSE.
If I could Mick, I’d like to expand a bit here to talk about the establishment rules because it’s a really important area we’re getting a lot of questions about. So companies must adhere to the GB and the EU BPR establishment rules. That means that for the GB market the authorisation holder must be established in UK, but for the Northern Ireland market they must be established in the EU or Northern Ireland. For the GB market, there is a one year “period of grace” or transitional period ending on the 31st December this year for products already authorised. So if you’ve already got a product authorised you’ve got one year to make sure that your authorisation holder is indeed established in the UK. If an application had already been submitted into the EU programme, but a decision wasn’t made by the end of the transitional period, then companies would be resubmitting those applications to us and the establishment rule must be met by the time we’re ready to authorise that product.
Then the third option is, if you are submitting a completely new application to us under the new GB rules, then the establishment rule must be met at the time of making the application.
Just coming back to the Northern Ireland situation, the establishment rule should already be met now so for products that are already authorised, that establishment rule should already be in place. We are aware that this has come as quite a surprise to some so we are making no immediate plans to start revoking products where this obligation hasn’t been met, but we are asking companies to get on with this and to get this in place as soon as possible. For meeting the establishment obligation in GB or NI, companies may have to apply to us to make a change and if companies are familiar with applying for change applications, that’s exactly what they would do, again using our new forms as I just explained before.
And then just one last thing – sorry this has been a very long answer – companies can apply to HSE for authorisation in GB and Northern Ireland at the same time using the one application form if this route is relevant to both GB and Northern Ireland. We hope that will be a bit of a saving where there’s only one application needed, rather than two separate ones.
Mick:
Ok Nicola, one last question for you. The active substance in my disinfectant product is due to renewal in the EU. Does HSE intend to conduct an independent review of active substances for biocides and if so, will the EU BPR deadline date for all active substances to be reviewed by 2023, be the same as GB BPR?
Nicola:
Right, of course GB is outside of the EU review programme and we will responsible for taking decisions on active substance nationally ourselves. So we will set up and undertake our own review programme for existing active substances. The timelines for the GB active substance programme haven’t yet been decided and we will consider these once we know the extent of the work for the GB review programme and we will know that once the resubmission deadlines have passed and these deadlines are the 31st of March and 29th June this year. So it’s only after those dates that we will have a feel of the extent of the work and we will start consider starting prioritising deadlines, approaches etc, etc. The good news is that in the meantime Article 89 of GB BPR continues to apply and this allows via resubmission products containing active substances supported in the review programme to continue to be made available while the active substances are still under review.
Mick:
Great thanks Nicola. That was Dr. Nicola Gregg who’s Team Leader for Biocides Operational Policy in HSE’s Chemicals Registration Division.
Andrea Caitens is one of the Team Leaders and a Regulatory Scientist from the Chemicals Regulatory Division covering REACH, CLP and PIC, that’s Prior Informed Consent. Andrea good to speak to you again. I have an email here. I am a small business that imports chemical products from other countries. Will I have ‘importer status’ obligations when importing substances into GB from the EU/EEA?
Andrea:
The simple answer is yes. GB based companies will have importer obligations where they import s
After UK Transition: Working with Chemicals - Episode - 5 - CLP, REACH, PIC and Industry voices
In this instalment, we invite two industry voices to discuss changes to Classification, Labelling and Packaging (CLP), Registration, Evaluation, Authorisation and Restriction of Chemicals (REACH) and Prior Informed Consent (PIC) regulations. We also explore the actions they have taken to keep their businesses moving following the end of the UK transition period.
If you have any concerns regarding UK Transition and the changes to REACH and CLP regulations, contact HSE at the earliest opportunity via ukreach.clp@hse.gov.uk.
If you have any questions regarding UK REACH enforcement, please contact the HSE at the earliest opportunity via CRDEnforcement@hse.gov.uk.
Podcast Transcript
Good day and welcome to episode 6 of the HSE podcast with me Mick Ord. Over the past few months we’ve been discussing the key regulatory changes which have been implemented now that the UK has left the European Union. In the last episode we heard from businesses about how they had been preparing for changes to PPP (Plant Protection Products) and BPR – Biocides Products Regulations, in the run up to 2021.
This time round we’re looking at how people have been preparing for the changes to CLP, that’s the Classification, Labelling and Packaging of substances and mixtures, REACH – that’s the Registration, Evaluation, Authorisation & Restriction of Chemicals, and PIC – Prior Informed Consent, now known as GB PIC, which concerns the import and export of hazardous chemicals.
John Mackenzie, Head of Regulatory Affairs at Thomas Swan in County Durham, is back with us I’m pleased to say, as is a new guest on the podcast Dr Chris Howick from Inovyn Chlorvinyls in Runcorn. They produce mainly chlorine, caustic soda and chlorinated derivatives from plants in the UK and all over Europe. They employ a total of 750 people. I started by firstly asking Chris about the challenges his company faced in the run up to 2021 as they prepared for the new GB regulations.
Chris:
Well I think it’s been an interesting journey from the very announcement of the referendum result. It caused a lot of discussion in the early days but I think bit by bit as regulations started to come in the UK and preparedness from the regulatory agencies in the EU progressed, it was a little easier to see exactly what we had to do. I think we had a few stop start processes with the no deal scenarios because we had to get ready to transfer REACH registrations and Biocides registrations across to a European entity or an ongoing European entity for the initial leaving dates and of course we had two or three leaving dates in the end and so we then had to cancel those transfers to bring them back to ensure that they didn’t transfer. So it’s been quite eventful in that respect but I think to a certain extent it didn’t matter whether there was a free trade deal or not because we were going to have to go through these actions anyway, so I think it gave us a little bit of extra time preparing it and I think now that that is done we can concentrate on the actions for ensuring that we are compliant with the new UK regimes where there’s a little bit of a grace period before the first sets of deadlines come up with that.
Mick:
John Mackenzie, was that a similar scenario at your company, in terms of ensuring that your products are REACH compliant?
John:
Indeed it was, yes very similar. I remember contacting some of our suppliers, the smaller guys especially and kind of like the rabbit in the headlights reaction from them like – what you mean we’ve got to change and do things that we didn’t do before, but now it’s gone from there to their saying yes, that’s fine no problem. So we’ve come on a huge journey from the referendum in 2016 wasn’t it – to now by the time this comes out – we will have left and it’s come from not knowing very much at all about what we are going to have to do to being pretty comfortable that we are on top of things. So yes, it’s been quite a journey.
Mick:
Chris, for you in terms of Classification, Labelling and Packaging, CLP, any observations about how the transition period has gone in that particular section?
Chris:
I think it’s been a little more straight forward, than the REACH situation, the advantage is although we now have two regulatory regimes, we manufacture at sites throughout the EU but we have a significant presence in the UK and so as far the UK manufacturing assets is concerned, we now have two regulatory regimes, one in the UK and one in the EU. The advantage is, of course, that we start with the same situation for classification and labelling because clearly on the 31 of December 2020, the UK had the European CLP regulation and this now transfers to the UK one. It remains to be seen whether there is differentiation and whether it happens and then to what extent it happens but there are some subtleties in that clearly when we supply companies in the EU from our UK site, those companies often become the importer and so they carry some additional responsibilities by importing material from outside of the EU into the EU and it works the other way round as well. If we import from one of our sites on the Continent, we now have to ensure that there’s reference to the UK or I should say GB classification regulation there as well and as I say at the moment, we start with the same classification so it’s a technical or administrative task, but we just need to see how that develops in the future and whether the UK will deviate or have a different opinion on a case by case or chemical by chemical basis.
Mick:
And how did you know that the various actions you describe were required? Where did you go for that information?
Chris:
Well, we’re very fortunate in that we play an active role in the Chemical Industries Association and also on the polymers side from the British Plastics Federation, so we’re active in those two trade associations for the chemicals and polymers side of our business. They’ve both been a very good source of information so the regular meetings and organisations of webinars with input from the UK regulators. On the European side actions, there has been some good, detailed guidance documents on the European Chemicals Agency website as well as the change in obligations from companies and the particular guidance on how you had to navigate through what’s termed the REACH IT, which is the Agency’s submission portal for chemicals as well as what the obligations for companies were for that, particularly on the REACH side rather than the CLP side. And then, of course, we did get the statutory instruments which of course are phenomenally difficult to read because they refer to the original European legislation. They only really highlight what changes by making them a UK regulation. I think companies, particularly on the continent that found the UK Statutory Instrument thinking they were going to find how they had to comply and it’s very, very difficult to read even if English is your first language. I think it’s the guidance that goes with it now and certainly the Government website has got a lot more information on and the HSE and Defra have done some very good roadshows over the last two or three years that have been very informative and I think recordings of those are still available on the internet if companies want to catch up with those. Those were particularly useful and I would say a lot more informative in the early stages than the initial guidance, but certainly we’ve now got some good documents from the UK regulators as well.
Mick:
What about the situation in terms of the export and import of hazardous chemicals – PIC?
Chris:
The Prior Informed Consent side has taken us a little longer to set the systems up because we weren’t sure exactly how the UK was going to do it but with materials transferring between our sites in the EU and our UK sites and vice versa, of course what would just be a seamless transportation before the end of the transition period, now has to be licensed and because the UK is now out, we did have to essentially apply for licenses before the end of the transition period in order to ensure that we had the necessary licenses for export. ECHA, the European Chemicals Agency work on a 35 day lead time for PIC applications, so those all had to be submitted well in time for the end of the year to ensure that they were in place.
Going the other way, the UK system is more based on seeking permission and authorisation via email. The UK has a system which is fit for purpose because of the smaller size of the market. I don’t think it’s gone for this extensive IT system that there is on the European side, but I think we’ll see how that goes in the HSE and the Competent Authorities in the UK, I think we’ll keep that under review as to whether it needs to be expanded, but again we had to set those up to be ready for the exports to go in January. We are confident that things are in place and we’ll review it as the New Year progresses.
Mick:
John, PIC doesn’t necessarily apply to you does it? What about CLP and REACH – have you got anything to add?
John:
In terms of preparations we’ve made do you mean? Technically, we are a medium sized enterprise and we don’t have any footprint in the EU, we don’t have an office or another site so what we had to do was to set up a relationship with what’s called an Only Representative or OR for short in the EU so we’ve done that with a German company and it’s a consultants again and what’s going to have to happen is – we transfer our REACH registrations to them first and they then accept them (in the New Year) and that will be our registrations transferred into the EU and then we’ll have to grandfather those into the UK system so it will end up with is REACH registrations in the UK and the EU. Of course we will only need those in the EU for chemicals th
After UK Transition: Working with Chemicals - Episode - 4 - PPP, BPR and Industry voices
In this instalment, we invite two industry voices to discuss changes to Biocidal (BPR) and Plant Protection Product (PPP) regulations and explore the actions they have taken to keep their businesses moving following the end of the UK transition period.
It should be noted that the views of any guests on HSE podcasts/recordings do not necessarily reflect those of the HSE or the wider government. Moreover, further website guidance was released in the time following the recording of this podcast. For the most up to date guidance relating to EU Exit, visit www.hse.gov.uk/brexit/chemicals-brexit-guidance.htm or email EU-exitchemicals@hse.gov.uk
Podcast Transcript
Welcome to the HSE podcast with me Mick Ord. I hope you’re well and looking forward to happy and prosperous year.
In the past few episodes we’ve been hearing from some of HSEs and DEFRA’s own EU regulatory experts about many of the changes that businesses face, now that the UK has left the European Union, and how they should prepare for it, but for this episode and the next one, it’ll be a bit different.
We’ll be hearing from the businesses themselves about what the past year has been like for them as they try to plan for life outside of the EU. The views of people whose businesses are being affected on the ground provide much food for thought and I’m confident that some of the things that they’ve observed will be ringing true for many listeners to this podcast. What they say will also hopefully help to steer you in the right direction as you maybe tackle some of the hurdles that they’ve been negotiating.
In today’s podcast we’ll be hearing from John Mackenzie, the Regulatory Affairs Manager at the long-established chemicals manufacturer Thomas Swan. They’re a family owned and run business with a UK base in Consett in County Durham, directly employing around 170 people with other bases in the USA and China. Also joining us is James Clovis, MD of London-based Gemini Agriculture – a company which specialises in the supply of agrochemicals to the UK market. James founded the company five years ago.
In this episode I’ve been talking to John and James mainly about how they‘ve been preparing for the changes in the regulations pertaining to PPP – Plant Protection Products – and BPR - Biocides Products Regulations. First of all I asked John what it was like for his company navigating the transition period last year.
John:
In the beginning it was pretty difficult really because there was so little information. I have to say that one of the immediate impacts of the vote to leave the EU was actually positive for us because the exchange rates changed and we were able to export more because we became more competitive in some markets and so actually it was a help in the beginning but the regulatory burden is going to be massive because of having to deal with two regulatory authorities – ECHA in Europe and HSE in the UK, but navigating it we just had to find whatever information was out there and initially there wasn’t much.
We’ve have kept in close touch with the Chemical Industries Association, the CIA and they’ve been brilliant with keeping us up to date. We’ve had regular meetings with them and they’ve organised meetings with the Government Departments BEIS, (Government department for Business, Energy and Industrial Strategy) Defra, HSE and so on, that’s been our main way of navigating it and finding our way through, up until more recently when more information has come out from Government departments. The impact is mainly going to be dealing with two regulatory authorities like I said. The regulatory burden is going to be increased in a department where there are only two of us working on regulatory issues. It’s going to mean quite a lot more work for us and therefore more cost.
James:
I think John’s nailed it there on the regulatory side. We’re quite lucky in Gemini because we primarily sell only in the UK. I think from an import and export point of view that’s where it’s going to impact us the most. A lot of the technical material comes from India and China which we can’t manufacture within Europe and within the UK and I think it’s going to have a fundamental impact on how we bring products in, you know what processes and what systems we have to work with and also how the parallels go and the extension. The extension of the active materials for three years is going to be very beneficial in one way. It kind of gives the UK a bit of longevity in certain products but it’s also going to have a delay because ECHA was dealing with a lot of the Annexe I and Annexe II renewals and I think what’s going to happen now is that we’ll see delays and I think even for generics as well as the multi nationals, we are kind of locked out of those chemicals whether we can access them from a competitive point of view or just from a multinational trying to modify any of their registrations, they’re going to be locked out for an extended period of time.
Mick:
And how can you prepare for something like that?
James:
Well it’s interesting. I think that from an import/export perspective, I think a lot of people have brought product into the UK whether it’s technical material or finished goods. I think we’ve seen an increase in product being brought in and stored. I think we’ve seen an increase in utilisation of certain Toll Manufacturers, there’s an awful lot of those being locked up very early on now. So I think primarily there’s a lot being brought into the country and is sat in warehouses and I think there are other preparations being made, but it’s trying to be informed as you possibly can and myself and Gemini – we’ve spent a lot of time working with forwarders and the importers trying to make sure that any documentation or approvals that they need, have been submitted well in advance.
For Northern Ireland we’ve applied for an EORI number extension, the X number I believe it is now and so we are trying to do everything we can but again, we don’t know all the answers yet so it’s trying to prepare as best we can when something pops up, you’ve got to jump on it as quick as you can.
Mick:
John what actions have you taken or at least started to take to ensure your products are biocide compliant?
John:
The main thing we’ve done, well a couple of things really, but one of the big things is that we’ve recently transferred – there’s a thing called the Article 95 list which is a list of active biocides that are allowed to be used in the EU, and so because we are out of the EU now, we had to transfer our registration on that list over onto our representative in the EU. Now of course being a small company, we had to use a consultant to do that and of course they don’t come cheap, so they are now going to become our representative in the EU working on our behalf and so we are now listed still on the Article 95 list, but with a representative in place rather than have a direct registration ourselves.
The other thing we’ve done though, as a company we’ve decided as a mitigation against the potential border friction that will no doubt occur, we decided that we would apply for a thing called AEO which is Authorised Economic Operator, something which is much more common in Germany and some other European companies but not so common here. I think the last count I saw was about 700 companies registered in the UK whereas there are about 10,000 or so in Germany. Anyway, we did that, it was a lot of work but it means that now we are registered on that scheme, that should help with our paperwork, it should reduce cross border friction between UK and EU, but also within the EU itself so it means that the red tape is cut out to a large extent and means we can deal more directly with our customers in the EU.
Mick:
And James what about you on that score – what actions have you started to take?
James:
What we’ve basically done is, all our registrations are UK Article 34 registrations, we have a couple of parallel imports as well. So as it stands most of ours will be compliant to the new system and we won’t need to do anything.
I think REACH is a slightly different kettle of fish and I think moving forward it’s going to take – it depends how you approach it – I think there’s going to be quite a lot of work for certain companies to make sure that all of the intermediates or components are registered in time. We’ve started working with the supplier of the intermediates and also the Toll Manufacturers as well to make sure everything is REACH compliant when we know exactly what we need to do going forward for that.
Mick:
We’ll be touching on REACH in the next episode. James what about PPP compliancy?
James:
As I alluded to earlier, all of our products are already registered with CRD/HSE and we expect that there won’t be much change going forward to the existing registrations. Going forward for new registrations though, that’s going to be interesting to see if there’s much change at all. One, to the documentation or requirements but also I think, as I mentioned earlier, to see what happens with the delays on the Annexe I, Annexe II renewals. From actions there’s not much we can do now, we are basically sat in a holding pattern for certain products waiting for the protection to come down so we can apply for registrations. There’s not a whole lot on the action side that we need to prepare for.
Mick:
So it really is the information that you need isn’t it? That’s what you’re looking for and then you can take your actions. So far, where have you been getting your information from, John you mentioned about the trade body before. Do you visit the HSE webpages for example?
John:
Yes, I have done. I have to say until recently at least, the HSE webpages weren’t terribly helpful, but they’ve now improved that dramatically. Recently, I was having a look at them and they’ve made a big change in
After UK Transition: Working with Chemicals - Episode - 3 - CLP, REACH & PIC
In this episode, we are joined by Alun Williams, Lead for External Comms and Stakeholder Engagement from the Chemicals team at DEFRA and Andrea Caitens, CLP, PIC and REACG Transition Programme Lead, Future Readiness at HSE.
We discuss the key differences between EU to UK REACH, the roles and responsibilities in UK REACH actions that people and businesses need to take in relation to CLP and PIC.
Visit our website for further information and guidance on CLP, REACH and PIC.
For any queries, get in touch via REACH & CLP: ukreach.clp@hse.gov.uk PIC: ukdna@hse.gov.uk
Podcast transcript
Welcome to the Health and Safety Executive podcast with me Mick Ord. I hope I find you in good health. This is the fourth in our series of podcasts designed to guide you and your business safely through some of the regulatory changes which are coming in at the end of the transition period.
Over the past few weeks we’ve looked at BPR and PPP and this week we’re looking at a total of Three Regimes in the one episode – REACH, CLP and PIC.
REACH is of course the Registration, Evaluation, Authorisation and Restriction of Chemicals ; CLP is Chemicals Classification, Labelling and Packaging and PIC is Prior Informed Consent for the export and import of hazardous chemicals, all three of which will change to varying degrees at the end of December 2020. So whether your company does business in Scotland, Wales, Northern Ireland or England we’ve some important information to relay to you.
After we’ve heard from our two experts, I’ll be giving out some important info about where you can find out more on what we’re talking about in this episode and also how you subscribe to our free eBulletin service so you’re kept in touch with news and developments as they happen.
For this episode, I’ve been speaking to Andrea Caitens a regulatory scientist from the HSE’s Chemicals Regulatory Division. She’s also the CLP Lead in the Transitions Programme Team. We’ll be hearing from Andrea shortly about the changes to CLP and PIC, but first from Alun Williams who’s the Lead for External Comms and Stakeholder Engagement from the Chemicals Team at DEFRA. He’s been telling us about the changes to the UK REACH regulations.
Alun, you say on your website that the key principles for REACH are retained – so what are these principles?
Alun:
The regulatory framework that we are putting in place for UK REACH will retain both the fundamental approach of REACH with its aims of ensuring a high level protection of human health and its key principles of REACH.
These include the “no data, no market” principle, the “last resort” principle on animal testing, access to information for workers and the precautionary principle as well as the provision for Only Representatives otherwise known as O.Rs.
Mick:
What are you doing to mitigate costs to business?
Alun:
Well, we are keeping the transition to UK REACH as simple as possible, avoiding change for change’s sake. For example, in building the Comply with UK REACH IT system, we have made sure it will work very much like the ECHA owned REACH-IT, including the same software requirements and many of the processes that businesses have been using and understand.
We have put in place “grace period of provisions” of “Grandfathering” and “Downstream User Import Notifications” to minimize the costs for businesses and maintain market access to both the EU and UK market.
Following concerns raised about the current timelines for supplying data to the UK regulator, we have decided to extend these deadlines which would enable industry to mitigate costs without reducing important environmental and health protections.
Mick:
Will UK business still be able to access the EU market?
Alun:
Yes, GB-based businesses wanting to place a chemical on the EU market will need to get that chemical registered with the European Chemicals Agency or ECHA. That registration must be held by an organisation based in the EU.
GB companies wishing to expert chemicals into the EU/Northern Ireland after the end of the transition period would need to rely on their EU/Northern Ireland based customers to register as importers or they would need to transfer their registrations to an EU/Northern Ireland based legal entity or Only Representive. ECHA has published guidelines on this.
Mick:
What changes Alun, are being made to the data submission deadlines?
Alun:
We have extended the existing data submission deadlines, set in legislation, as follows.
The initial notification stage for UK downstream users to submit Downstream User Import Notifications or DUINs, as they are colloquially known, has been extended from 180 to 300 days from 1st January, 2021. As a result, UK downstream users will have the opportunity to assess how existing EU REACH registrants have met the 120 day deadline and use it to inform their own process.
We have also extended the deadline for completing a full registration supported by full data packages to 2, 4 and 6 years from the end of the initial 300 day period. The deadline for final submission of data underpinning the full registration is dependent on tonnage bands and hazard profile, with the highest tonnage bands and most hazardous chemicals first.
Mick:
Will Northern Ireland be part of UK REACH?
Alun:
So, for the duration of the Protocol, Northern Ireland will remain part of the EU regulatory systems for chemicals to ensure frictionless movement of goods within the island of Ireland, whilst remaining within the UK customs territory. We are also offering a streamlined process for Northern Ireland chemicals to be notified with UK REACH to facilitate trade from Northern Ireland to Great Britain. Northern Ireland businesses can notify direct should they wish to do so; otherwise the responsibility will lie with their GB customer.
Mick:
When will companies be able to access the appropriate forms on the website?
Alun:
These will be available when the Comply with UK REACH IT system goes live from the end of the transition period.
Mick:
What will be the functionality of the UK REACH IT system?
Alun:
The Comply with UK REACH IT system will replicate key functions of the EU REACH IT system to provide continuity for GB businesses. At the point of launch, businesses will be able to use the service to validate existing GB held EU REACH registrations so Grandfathering, as we discussed earlier. They’ll be able to submit Downstream User Import Notifications. You’ll be able to submit a new substance registration. You’ll also be able to submit new product and process orientated research and development – PPORD – notifications.
Mick:
Is the information they need to supply to the HSE different to the previous requirements in either quantity or nature of content?
Alun:
It’s important that people consider what their new roles are within UK REACH. So for example a lot of the information will be exactly the same, but perhaps their roles within the process have changed. So for example if you were previously a downstream user you may now have importer obligations under UK REACH. We strongly recommend that you go to the HSE website and read the guidance there as to identify what information you’ll need to supply.
Mick:
Andrea, CLP as we know refers to the Classification, Labelling and Packaging. In 2021 after transition the legislation changes to GB CLP – what are the main changes which will happen?
Andrea:
Businesses based in Great Britain that place chemicals on the GB market and that’s both substances and mixtures, will have to comply with the GB CLP regulation and this will also apply to those suppliers based in Northern Ireland who supply directly to the GB market.
However, it’s important to know that the majority of CLP Regulation remains unchanged and the main duties to classify – that is to identify the intrinsic hazardous properties and communicate information about those hazards through labelling and to securely and safely package those chemicals will all remain the same.
From the 1st of January, 2021, Great Britain mandatory classification and labelling or GB MCL, will replace the EU harmonised classification labelling system and Great Britain will make its own decisions about mandatory classification and labelling. All of the existing EU harmonised classification and labelling at the end of the transition period, will be kept as GB mandatory classification and labelling and GB suppliers will need to comply with MCL in the same way as they did with EU harmonised classification and labelling before.
Those substances with a GB mandatory classification and labelling will be included in the GB MCL list and this will be hosted and managed by HSE as the GB CLP Agency. GB-based suppliers supplying in the Great Britain market with chemicals and Northern Ireland based suppliers who supply directly to the GB market will deal with HSE as the GB CLP Agency instead of the European Chemicals Agency or ECHA and this will include when notifying substances to the GB notifications database and for submission of requests to use alternative chemical names.
There will be new requirements on GB-based companies currently identified as downstream users and distributors that is those who are currently supplied by businesses in the EU/EEA. These GB-based downstream users and distributors will become importers under GB CLP after the end of the transition period if the same supply arrangements continue and as such they will have to comply with all the importer’s duties and obligations.
Further information is provided in the scenario table which is currently available on the HSE website.
Mick:
Will this effect businesses exporting to the EU/EEA?
Andrea:
In order for a GB- based exporter to supply chemicals to the EU/EEA, they must identify and importer. There is no allowance in either the EU or GB CLP Regulations for a third party to act on behalf of the imp
After UK Transition: Working with Chemicals - Episode 2 - BPR
In this episode, we are joined by two HSE experts in Dr Nicola Gregg - Biocides Operational Policy Team Leader and Dr Pierre Cruse - International Chemicals Unit Team Leader.
We discuss the changes that will have the greatest impact on businesses following the end of the UK Transition period, how to get an active substance approved in both the EU and GB and how companies can get on the GB version of Article 95.
Visit our website for further information and detailed guidance on biocidal product regimes.
If you have any concerns regarding UK Transition and changes to Biocide regimes, contact HSE at the earliest opportunity via biocidesenquiries@hse.gov.uk
Podcast Transcription
Welcome to the latest HSE Podcast with me, Mick Ord. This month, with the help of our resident experts, we’ll be guiding you through the new Biocidal Products Regulations – that’s BPR to you and me - and how the new regulatory framework will affect your business as we leave the EU and the transition period comes to an end.
We’ll be finding out what you should be doing now and will be required to do in the future under the new GB regulations and how that will affect companies in Great Britain and Northern Ireland.
Now we’ve left the EU, many of the functions currently being carried out by Europe will soon be transferred to Great Britain but certain EU functions have been removed and we’ll be highlighting these areas and explaining what you need to do to make sure you comply with the new arrangements. Over the next half hour or so we’ll be addressing many of the issues that are concerning businesses and pointing you in the right direction - so without further ado, let me introduce you to 2 people whose knowledge of the new BPR framework is second to none. Dr Nicola Gregg and Dr Pierre Cruse are both from the HSE. Nicola is team leader for Biocides Operational Policy in the HSE’s Chemicals Regulation Directorate and Pierre is team leader at the HSE’s International Chemicals Unit – his team is responsible for developing Government policy on biocides and also the CLP regulations – that‘s the classification, labelling and packaging of substances and mixtures.
I’ll start with you if I may Pierre - Will the new GB framework for Biocides be the same as the EU framework?
Pierre:
I think the answer is in some ways yes and some ways no. From the 1st January next year, 2021, Great Britain is going to have its own independent regulatory framework for biocidal products. It’s going to reflect the current EU framework, the EU Biocidal Products Regulation, but they are going to operate independently of each other. Essentially, the rules and standards are going to be pretty much the same, but some elements to the framework won’t exist, basically those bits that refer to EU processes and institutions that we’ll no longer be dealing in the national system.
Mick:
So in what areas will it be different?
Pierre:
The Great Britain Biocidal Products Regulations – BPR – we call it a lift and shift of the EU’s BPR. What that means essentially is that we copied it into domestic law without any policy changes. The only bits that have changed are those which wouldn’t operate correctly in the new Great Britain context, as I say, the bits that refer to European Institutions, the European Chemicals Agency and the European Commission are examples of that. So for example ECHA, functions that previously sat with ECHA are now going to be transferred to Great Britain bodies, where we are still doing them, and commission decisions which used to be taken by the European Commission, they are now going to be taken by the Secretary of State with consent from Ministers in the Devolved Administrations.
Mick:
So what changes will have the greatest impact on businesses?
Pierre:
I’ll just run through some of the biggest changes and impacts for businesses. Perhaps the main one is if a company wants an authorisation in both the EU and Great Britain after the end of the transition period, they’ll need to apply separately to both the EU through ECHA and Great Britain. That also means that future European active substance approvals and product authorisations, won’t be valid in Great Britain and vice versa.
A similar thing applies to active substance approval. If you want an active substance approval in Great Britain at the end of the transitional period, you need to apply separately from any application you may be making in the EU. The other thing is that authorisation processes for biocidal products that used to apply across European member states, won’t apply any more to Great Britain. That means there’ll be no more mutual recognition of product authorisations between the EU and Great Britain. EU Union authorisations won’t be valid in Great Britain after the end of the transition period and also you won’t be able to use a simplified authorisation that you had in European Union to put a product on the market in Great Britain after the transition period either.
Another key thing that businesses need to be aware of is that HSE won’t be using ECHA’s IT tools, the main one being the register of biocidal products R4BP3 after the end of the transition period.
And we won’t have access to ECHA’s databases anymore and what that means is that applications for biocidal product authorisations have to be sent directly to HSE, not using R4BP3 and using the HSE application forms that we’re going to put in place. The other thing related to this is that for active substances and products to be supported in Great Britain – if you want to make an application, all the relevant data will need to be resubmitted to HSE, even if you’ve previously submitted it to ECHA. There are transitional arrangements in the legislation that will tell you exactly when you need to do this and we’ll explain that later in this Podcast.
Mick:
Thanks Pierre. Over to Nicola then. When will the new application forms and process details be live on the HSE website Nicola and will they be different to the old forms?
Nicola:
Well we are completely rewriting all of the information on our website including the application forms and all of this will be published by the 1st of January. Application forms and data will be submitted to HSE, not via R4BP as Pierre has just said but instead by HSE’s upload link and this is a secure, cloud-based platform for sharing files. Because of the lift and shift that Pierre has also mentioned, the information required is pretty much the same as companies are used to and the data requirements are also the same.
Mick:
Will Great Britain have its own review programme?
Nicola:
Yes, after the first of January, 2021 of course, GB will be responsible for taking our own decisions on active substance approvals at our own national level and because of this, we will establish our own review programme of existing active substances. It’s important to note that Article 89 of both the EU BPR and the new GB BPR will continue to apply. This means that as happens now, products containing active substances which are within the scope of the GB review programme can continue to be made available on the GB market while those active substances in the products are still under the review.
Other rules for participation and withdrawal from the review programme will also continue to be similar to what people are used to under the EU review programme such as things like taking over role of participant.
Another issue worth pointing out here is that the priorities and the timelines of the review programme, in the GB review programme, have not yet been determined and we won’t be in a position to make those determinations until we know what the total support of active substances within GB actually is.
Mick:
Thanks for that Nicola. Well, after the transition period HSE will no longer have access to the ECHA databases. What are the implications for businesses here in the UK?
Nicola:
That’s correct. After the 1st January, 2021 GB will not be permitted to access confidential information held by ECHA. This means that any data or information that companies previously submitted via these processes will no longer be available to us here in HSE for us to refer to, so the data will need to be resubmitted to us so that we can continue operating our own national regulatory regime. There are deadlines for resubmission of the data and these are set out on our new GB BPR transitional arrangements and these are legally binding. Now, HSE appreciates that the requirement for applicants to resubmit their data packages may result in an increased cost to businesses and so we are not going to charge for the work that’s necessary in the resubmitting of the data and I am talking about just the actual resubmitting and all that’s entailed around that, not the eventual evaluation of the data by us.
Mick:
Will the data required by the HSE be the same as that required by ECHA?
Nicola:
Yes it will. The technical data requirements which must be addressed to support both the approval of an active substance and the authorisation of a biocidal product under a GB regime, will be the same as those specified under the EU regime.
Mick:
What’s the situation for companies which already hold the biocidal product authorisation in the UK under EU BPR – will that still be legal in the UK after the transition period?
Pierre:
Yes it will. Any biocidal product authorisations and also any active substance approvals that were in place before 1st January, will remain valid in Great Britain all the way through to their expiry date whatever that was. However, there are a couple of additional requirements which authorisation holders for biocidal products need to be aware of. The first is that they need to be established in the UK within a year of the end of the transition period that’s by the 31st of December 2022 to continue holding that authorisation and the seco
After UK Transition: Working with Chemicals - Introduction to the series
In this introductory episode, we discuss the main changes to how chemicals will be regulated in the UK from 1 January 2021 and how HSE can help your business prepare for the end of the transition period. We also discuss the different areas and topics that will be covered during the series.
Visit our website for further information and detailed guidance on the chemical regimes.
*The information in this podcast was correct at time of publication.
Podcast Transcription.
Welcome to a new series of podcasts from the Health and Safety Executive aimed at helping businesses that work with chemicals. Everything you need to know before and after the end of the transition period.
My name is Mick Ord and over the next few months, I’ll be your guide through some of the changes which are happening as a result of the UK leaving the European Union.
We’ll be releasing a difference episode of our podcast every month or so until the New Year and we’ll be hearing from a range of experts about what you need to do to make sure the transition goes as smoothly as possible for you and that if you hit any obstacles, we’ll point you in the right direction so you get the right answer as soon as possible. In short, we’re here to help you so subscribe to our podcast, especially if you’re a newcomer to podcasts. Believe me it’s dead easy.
The information we’ll be giving you is important for over 200,000 businesses involved in the export and import of chemicals throughout the UK from the big multi-nationals to the small one man, or one women business.
Joining me today is someone who’s been living and breathing the changes in the legislation for the chemicals sector over the past 18 months and she’s going to talk to us about why we are launching this podcast and a little bit more detail about what we can expect over the next six months or so. Kayleigh Roberts is from the HSE and she works in the External Communications and Stakeholder Engagement Team, bit of a mouthful but - Hi Kayleigh, welcome.
Kayleigh:
Hi Mick, thanks for having me.
Mick: Our pleasure. First of all, why has the HSE decided to launch this podcast because it’s not something that you’ve done before is it?
Kayleigh:
That’s right Mick this is not something the HSE has done before and in order to help businesses help prepare themselves get ready for the end of the transition period, we want to make sure that we are making as much information available in as many digestible forms as we can to help businesses understand the duties and obligations that they may need to undertake from the 1st, January, 2021. So although it isn’t something we’ve ever done before, last year we did actually record a series of videos, however, owing to the current public health crisis, we believe that this is a more efficient way to provide information this time round.
Mick:
Yes, that makes sense. Now as I mentioned in the introduction, you’ve been living and breathing the transition changes over the past year or so, so can you just give us an idea about what you and your colleagues have been doing and what it’s been like being at the centre of these historical changes in legislation?
Kayleigh:
Yes, as you mentioned, this is something that has never happened before and it’s something that we’ve never had to take into account before so in order to make sure that we’ve got the legislation in place for businesses to take the duties and actions that they need to from the 1st, January, 2021 when the transition period ends, we’ve had colleagues whose primary role is to work on developing that legislation, to amend the previous statutory instruments that would have come in place in 2019 to take into account the Northern Ireland protocol. So this has been a joint effort of policy and operational colleagues across HSE and we’ve all been working together to make sure that that legislation is laid in Parliament to make sure it’s in place for the 1st, January, 2021.
We’ve also had colleagues working on future trade agreements between the European Union and also the rest of the world and that has involved a lot of trade and negotiation talks which are still ongoing as I speak. We’ve also had colleagues on the team working on governance, peer reviews and the strategy aspects and also, finally, the team that I work with the communications team, we’re making sure that everything that is taking place and the preparations that are being made for the 1st of January, 2021, are able to be communicated effectively to the stakeholders within the chemicals sector.
It’s been a mammoth effort, it really, really has. It’s brought together teams from other government departments and also been a mammoth effort within HSE itself.
There’ve been different teams within divisions within HSE which have been working together which may not necessarily have worked so closely before, it’s been a totally different way of working.
Mick:
It’s interesting you say that because we all watch about the EU and the Government, we all watch that on the news and we don’t really realise what’s going on behind the scenes. I think it is important that people do know that a lot of people have put a lot of work into this to make it smooth for the businesses. Now the stuff that we are going to talk about in the podcast today and over the next few months, is it applicable to businesses whether there’s a deal or no deal with the EU?
Kayleigh:
I think it is important to note Mick when you refer to deal or no deal is that the UK left the European Union on the 31st, January 2020 with a deal and in line with that deal, we entered a transition period which will end on the 31st, December 2020 so what is going on at this moment in time is preparations for either a negotiated future trade agreement or a non-negotiated future trade agreement, we don’t actually use the terms deal and no deal anymore and I know that that is something which stakeholders within the sector may find a little bit odd, if you will, to get their mind around because we’ve been using the term deal or no deal for a great deal of time but it is important to note that that is not the message which is going out anymore.
Mick:
OK, I will not be using that term again, don’t worry! Which sectors in particular are you keen to reach over the next few months?
Kayleigh:
HSE is involved directly in the regulation of biocides, we are also directly involved in the regulation for classification, labelling and packaging of chemicals and also the export and import of hazardous chemicals which is known as PIC, or Prior Informed Consent and HSE also has involvement in the Pesticides Regulation and also the REACH Regulation, so what we want to do is to target businesses who work in those five chemicals regimes. We want to target them to make sure they are aware of the duties and obligations that they may need to undertake.
Some of them might not have needed to have done before or may have not needed to have considered before so we want to make sure that they’ve got all the necessary information that they need to prepare for the 1st of January, 2021.
Mick:
And what are the timescales and deadlines for businesses who’ll be affected by the changes then Kayleigh?
Kayleigh:
So, across the five regimes there are actually different timescales that need to be taken into consideration to ensure that legal obligations are met and one thing which I would recommend is visiting the HSE website, we’ve got a lot of information with regard to deadlines that are in place. Like I mentioned, they do vary because what we’ve put in place as part of the regulation is something that we refer to as transitional arrangements and those transitional arrangements basically give businesses different amounts of time to comply with different parts of the regulations to make sure that they are safely using chemicals within the market in Great Britain from the 1st of January, 2021.
Mick:
Right, so all the information they require either is on, or will be on the HSE website?
Kayleigh:
Yes, there is a current version of guidance on the HSE website for all five of the chemicals regimes which I mentioned before and that will be constantly reviewed and updated as and when as and when information is available. We’ve also got a really widely subscribed e-bulletin service and that’s got over 220,000 members you know, that is a really well subscribed service. And we will make sure that any guidance changes or anything like that are also advertised via that route as well so that businesses can be aware that these changes are being made and that there’s new guidance available.
Mick:
Have many businesses already been in touch with HSE with queries? What are the areas they are particularly concerned about?
Kayleigh:
Concerns vary widely. You know I think a lot of businesses now are just wanting to start to make the necessary preparations that they can, which is why in part we are doing these podcasts. We are going to have subject matter experts for all of the regimes that are going to come and discuss the necessary preparations that businesses need to take by regime. I think businesses are just wanting to make sure that they are adequately prepared for anything that they need to do in the immediate term, after the 1st, January,2021. But also, things that they may need to start preparing for now. There may be duties and obligations which that come in six months after the end of the transition period that they may need to start taking preparations for now.
Mick:
What might be the consequences if businesses put off engaging with the HSE for another day because say they are too busy dealing with the everyday stresses and strains of running their own business?
Kayleigh:
I think that one of the main things that we should take into consideration is that HSE is the
Anybodyknow how can I get full subtitle of these podcast? Castbox just shows half of them
Anybodyknow how can I get full subtitle of these podcast? Castbox just shows half of them