Discover
The Future of Processes
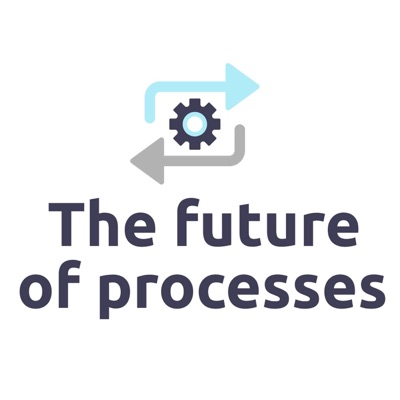
The Future of Processes
Author: Ben Merton
Subscribed: 2Played: 1Subscribe
Share
© 2023 The Future of Processes
Description
Unique perspectives from people in manufacturing about what it really takes to bring products to life. This is a podcast about building an organizational culture, leadership, product design, supply chain, change management, how to attract the best talent and in particular, how we can create better, more human processes for the factories of tomorrow.
16 Episodes
Reverse
Sarah Mauragis runs Continuous Improvement at Flow Rite Controls, which manufacturers, and markets fluid control devices for lead acid batteries, recreational fishing boats, laboratories, and medical uses.During high school, Sarah Mauraugis read an article in Seventeen Magazine about women in STEM, which set her on a course towards engineering. Today, she heads Continuous Improvement at Flow-Rite Controls, a manufacturer of fluid control devices based in Byron Michigan. Ben Merton talks ...
In this episode we speak to Stephanie Stuckey, a former state representative in the Georgia assembly and now CEO of Stuckey’s, a pecan log roll and candy manufacturer that was started by her grandfather in 1937 and sold to a conglomerate in the 1970’s. Stephanie re-acquired the company in 2019, turned the business around and is now determined to put Stuckey’s back at the forefront of roadside Americana. We also talk about:The history behind the Stuckey’s brand and why it was 6 figures in debt...
Gerald Heitmann, formerly General Manager of Quality Operations at Panasonic Energies North America joins Ben Merton to talk about how people like Edward Deming, Kaouru Ishikawa & Dr. Wheeler shaped his understanding of Quality and Continuous Improvement and why they are still relevant today. Gerald further explains where Lean Six Sigma falls short of helping people understand their own 'system of profound knowledge', and why AI is not going to bring about disruptive change in manufa...
In this episode, I speak to Gregory Ayers, the Director of Operational Excellence at Innovative Hearth Products, a manufacturer of indoor and outdoor fireplaces headquartered in Nashville. We speak about the importance of senior management in getting continuous improvement to stick and really impact the company in a meaningful way. We also talk about how CI has been turned into a farce and how it’s being undermined when leadership only provides lip service instead of an all out cul...
Chris Sidney manages quality, continuous improvement and metrology at the Winbro Group, a manufacturer of high-precision machining technologies in the UK, US and Taiwan. Starting his career in engineering as a Whitworth Scholar, Chris has spent more than 10 years managing quality and continuous improvement initiatives for the Winbro Group and Siemens Industrial Turbomachinery.I talk to him about the cultural differences between how people handle change and leadership in the US & UK, how p...
Tudor Sariou heads continuous improvement at Steam Whistle Brewing, which is a BRC certified brewery in Toronto that produces 90,000 bottles of beer a day and sells across the whole of Canada. In this episode, Tudor and Ben talk about the challenges that he's faced in driving quality and continuous improvement in food processing companies as diverse as Campbell's Soup and Club Coffee, along with these other topics:The challenges involved in driving continuous improvement across an organizatio...
Originally from Kenya, Robert Odhiambo came to the US over 15 years ago and has made a career of driving change and continuous improvement at companies like USPS, Ingersoll Rand, and Spectrum Chemical, an FDA registered manufacturer of chemicals and lab products. In this episode, Ben and Robert talk about:Why creating ‘flow’ is the key to creating customer satisfaction, whether you are in a Fortune 500 organization like USPS, Ingersoll Rand, or in industries as diverse as chemicals, phar...
In this episode Ben and Stephanie talk about The history behind the Stuckey’s brand and why it was 6 figures in debt when she bought the companyHow she runs a successful comeback brand despite having no background in manufacturing, business or candy makingThe pivotal change to the business she made that has helped her turn the company around to 7 figure profits in a year Her biggest failure at Stuckey’s that taught her to handle quality issues effectively and how to minimise time and resources spent in dealing with a problem to enhance customer satisfactionThe important advice she has for women in food and manufacturing that helps you see being female in this industry as your superpowerPractical advice for when you’re struggling to stay focussed on the big picture goals and how to implement a culture of continuous improvement Email Ben at ben@futureofprocesses.comVisit unifize.com to get your free trial
In this episode we speak to Alan Slater, the Director of Continuous Improvement at Value Added Products based out of Oklahoma. Alan shares how quick and simple changes can affect massive results (like increasing turnover by $3 million) and how to approach implementing changes so that people are on your side and not actively resisting new processes.Ben and Alan talk about How he reduced the scrap factor along the dough production line from 20% to just 2% by slowing down the process and saved the company over 9 weeks of wasted time annuallyHow a simple reorganization like going from a standard 1 hour break to a rolling break system generated over 1.2 million units and $3 million in revenue in one yearHow Alan was able to get product rolling out in just a few hours and reduced the standard 4 hour wait time resulting in an increased efficiency of 500%How to decrease your pit time so you can get the car on the race track more quicklyWhy digital transformation is the most obvious next step in terms of increased sustainability and reducing waste- the simplest example to consider being the 5000 page catalogs that most companies used to produce and how obsolete they are now.We hope this interview provides some food for thought and we'd love to hear your feedback. What do you want to hear about on the podcast next?
In this episode we speak to Gregory Ayers, the Director of Operational Excellence at Innovative Hearth Products. We speak about the importance of senior management in getting continuous improvement to stick and really impact the company in a meaningful way. We also talk about how CI has been turned into a farce and how it’s being undermined when leadership only provides lip service instead of an all out cultural transformation that includes quality and CI. Ben and Greg talk about How he was inundated with data and reports at his first job that made him regret not finishing college but he moved into quality engineering through sheer will, hardwork and a willing mentorWhy his advantage is his deep knowledge about operations, engineering and continuous improvement that helps drive forward customer centric processes that are as robust as possible without being over processedThe criticality of getting senior management to focus on a measurable result and metric to ensure your continuous improvement processes are addressing what they need toHow when the senior leadership starts running CI for the sake of it, the problem you're trying to solve becomes murky and the whole process becomes impossible to sustain The failed Kaizen event on the shop floor that made him realize the need for CI is not about Kaizen, six Sigma or what you read in a book, it's about the real world outcomes that the workers care about like uptime of a strapped and how it hinders their productivity to have a machine that constantly needs to be fixedHow his efforts to embrace environmental and green alternatives got him thinking about waste and why we do things the way we do. For example, are you just following orders because that's how it's always been done or is there a real, logical reason that's driving this process?We hope this interview provides some food for thought and we'd love to hear your feedback. What do you want to hear about on the podcast next?
During high school, Sarah Mauraugis read an article in Seventeen Magazine about women in STEM, which set her on a course towards engineering. Today, she heads Continuous Improvement at Flow-Rite Controls, a manufacturer of fluid control devices based in Byron Michigan. Ben Merton talks to her about the advantages of being a woman in a male-dominated world, how she builds and manages Flow-Rite's Kaizen funnel, and some fascinating insights into methods she uses to build a culture of continuous improvement.Episode SummaryWhy being a woman can give you an advantage over men to come up with creative ways to solve problems that men often overlook.How Flow-Rite's has boosted innovation by adopting a rule that every employee must submit at least one continuous improvement idea each year.How Sarah builds and maintains Flow-Rite's Kaizen funnel using Excel sheets and whiteboards to address the 8 wastes, reducing wastage of scrap, energy and other resourcesA deeper insight into the result of a Kaizen into how the company was using its inventory management system, and the problems that result from band-aid software customizations that often add unnecessary steps to repetitive computer-related work.Why the current and future shortage of labor in manufacturing will hopefully drive efficiencies in communication and team management.Automation needs a human touch: it's not good enough just to invest in the latest and greatest machine. You need to understand how your employees will interact with new equipment to avoid waste.How measuring the success of a Continuous Improvement project does not just come down to savings and improved material flow. It's when new ways of doing things come from within and happen without coercion.Continous Improvement is about shepherding from the rear. There's no such thing as a Continuous Improvement manager; you're really just a facilitator and cheerleader.Women should strive to overcome stereotypes and break the mould because manufacturing desperately needs diversity to solve its problems.
Deacon Wardlow is a self-described ‘New Tech Nerd’, who has spent a lifetime at the intersection of technology, manufacturing and continuous improvement. After leaving college in the US, he moved to Japan and was exposed to Toyota Kata, Kaizen, and Ishikawa.He talks to Ben Merton about the differences between the Japanese and American approaches to continuous improvement and what manufacturing companies can learn from software companies if they embrace disruption.Episode SummaryHow Vantage LED was able to build a culture of continous improvement using Agile and Scrum in a manufacturing environment.Why manufacturers really struggle with disruption and innovation: there is an inherent fear of failure, which is seen as part of the process in the technology world.How the decline of US manufacturing is a function of a collective failure to embrace disruption in manufacturingContrasting the efficiencies delivered by the Japanese culture of ‘sameness’ and equality across the organisation with the American mindset of ‘craftsmanship’.Why American individualism might inhibit the team building necessary to a well-run manufacturing operationWhile technology has already displaced certain jobs, this is something that will lead to faster improvements in people’s quality of life and work.How leadership is about helping people achived goals and giving them credit for that achievementWhy continous improvement is not a 9-5 job: it’s a mindset about helping people.
Gerald Heitmann, President of SDG Global and formerly General Manager of Quality Operations at Panasonic Energies North America joins Ben Merton to talk about how people like Edward Deming, Kaouru Ishikawa & Dr. Wheeler shaped his understanding of Quality and Continuous Improvement, and why they are still relevant today. Gerald further explains where Lean Six Sigma falls short of helping people understand their own 'system of profound knowledge', and why AI is not going to bring about disruptive change in manufacturing. Episode SummaryWhy certain elements of Lean Six Sigma are diametrically opposed to the principles of Edward Deming: Lean Six Sigma is focused on cost and not building a system of profound knowledgeHow Lean Six Sigma specifically fails to adhere to Deming’s 8th Point: “Remove fear from the system”. By dividing everyone into black belts, green belts and everyone else, it creates organizational boundaries that propagate fearWhy sub-systems like purchasing and finance are so important to your understanding of your organization’s system of profound knowledge…areas that are often outside the scope of a Six Sigma projectHow to implement SPC without spending millions of dollars on complicated software Why AI is just another tool (“A high-tech knob turner”). It is not a replacement for conventional quality improvement, which should remain in the control of humansHow 85% of all quality improvement problems are caused either by decisions or indecisions by managementThe future of processes is ultimately about humans enabled by a combination of software and Deming’s principles
Starting his career in engineering as a Whitworth Scholar, Chris Sidney has spent more than 10 years managing quality and continuous improvement initiatives for the Winbro Group and Siemens Industrial Turbomachinery. Ben Merton talks to him about the cultural differences between how people handle change and leadership in the US & UK. They also discuss how personality testing can be a useful part of creating the right environment for change, and how the Future of Processes will be driven by the need for more ethical and environmentally friendly processes and products. Episode Summary:The decline of UK manufacturing from 25% of GDP in the 1970s to 10% today and hopes for a resurgence as the government tries to bridge the skills gap by advancing STEM subjects and offering BTech qualifications instead of GCSEs.The differences in effecting change at a plant in South Carolina vs the UK: Americans are less suspicious of change than the British, and less likely to question leadership decisions.An overview of how Chris and his team used data to solve a challenging problem involving machined parts that were jumping in and out of tolerance.How analysis-paralysis is often the result of not defining the scope of an improvement initiative correctly in the first place.Why it’s important to have people with different personalities in the room to create the right environment for solving problems. Using online personality tests to understand your own personality and those of your colleagues can prevent building an echo chamber.How the previous experience of a given company's leadership with Lean and Six Sigma is the primary determining factor of whether it will be successfully adopted in any new initiative.The differences between Lean and Six Sigma: solving the same efficiency problem from different angles (waste and variation reduction).Advice for Lean Six Sigma enthusiasts: most people don’t care about your deep statistical and technical knowledge. Break it down for them into something they understand.How the Future of Processes is likely to be shaped by the need to solve ethical and environmental dilemmas. The removal of waste won’t be driven by greed and cost but by external regulations and changing consumer demands for greener products.
Originally from Kenya, Robert Odhiambo came to the US over 15 years ago and has made a career of driving change and continuous improvement at companies like USPS, Ingersoll Rand, and Spectrum Chemical, an FDA-registered manufacturer of chemicals and lab products. Ben Merton talks to him about how to build trust with mid-management employees who are resistant to change, and the importance of coaching upwards to senior leadership on new initiatives. Episode Summary:Why creating ‘flow’ is the key to creating customer satisfaction, whether you are in a Fortune 500 organization like USPS, Ingersoll Rand, or in industries as diverse as chemicals, pharmaceuticals or building materials.The importance of mapping ‘information flow’ as part of your Value Stream Mapping. Continuous improvement is not just about how material moves through the shop floor.How changing mindsets is the key to creating the right behaviour for implementing continuous improvement. To do this, you need to build relationships and trust outside of the work environment, especially with apparently difficult or intractable people.Coaching upwards: people often forget the importance of changing the mindsets of senior leadership at the beginning of a continuous improvement initiative.Where you are most likely to see resistance to change: mid-level management. To overcome this, you first need to listen and understand where people are before you start talking and making assumptions.Moving OEE from 52% to 88% in a plant by empowering a mid-manager who was previously resistant to change and building engagement with daily huddles.How the future of quality management will be about better usage and application of programming tools like Python to day-to-day requirements, more automation and better visualisation of continuous improvement KPIs.
Tudor Saroiu talks to Ben Merton about the challenges that he’s faced in driving quality and continuous improvement in food processing companies as diverse as Campbell’s Soup, Club Coffee, and now at Steam Whistle Brewing. We learn about the importance of employee happiness, how to win leadership over to continuous improvement initiatives, and what to do with people who are resistant to change.Episode summary:The challenges involved in driving continuous improvement across an organization with people from different geographic, educational and cultural backgroundsBringing alignment to continuous improvement objectives in production, packaging, marketing and sales.Specific ways in which he was able to get cross-functional teams to collaborate, including process mapping and building consensus.Ways to manage people who are resistant to change and how to make them feel that their voice is being heard.Why it’s so hard to get sales teams to cooperate on continuous improvement initiatives.The differences in building a culture of continuous improvement in large vs small companies.How to recruit people into quality and continuous improvement.Focusing on the ways that continuous improvement impacts the bottom line as a means to get buy-in from the C-Suite on new initiatives.Examples of how Steam Whistle was able to reduce fermentation time by 10-15% and free up tank capacity.How the future of processes will move towards automation without the need for layoffs because humans will focus more on areas where they add value.