GE Cypress Blade Tip Swap-out, Vestas Load Probability Control Method
Description
This week on Uptime Power-Up, a method from Vestas for modifying control of a wind turbine using load probability, a blade tip swap-out for Cypress turbines from GE, and a wind turbine tower with solar panels installed.
Sign up now for Uptime Tech News, our weekly email update on all things wind technology. This episode is sponsored by Weather Guard Lightning Tech. Learn more about Weather Guard’s StrikeTape Wind Turbine LPS retrofit. Follow the show on Facebook, YouTube, Twitter, Linkedin and visit Weather Guard on the web. And subscribe to Rosemary Barnes’ YouTube channel here. Have a question we can answer on the show? Email us!
Pardalote Consulting – https://www.pardaloteconsulting.com
Weather Guard Lightning Tech – www.weatherguardwind.com
Intelstor – https://www.intelstor.com
Wind Energy O&M Australia Conference – https://www.windaustralia.com
<figure class="wp-block-image size-large is-resized">
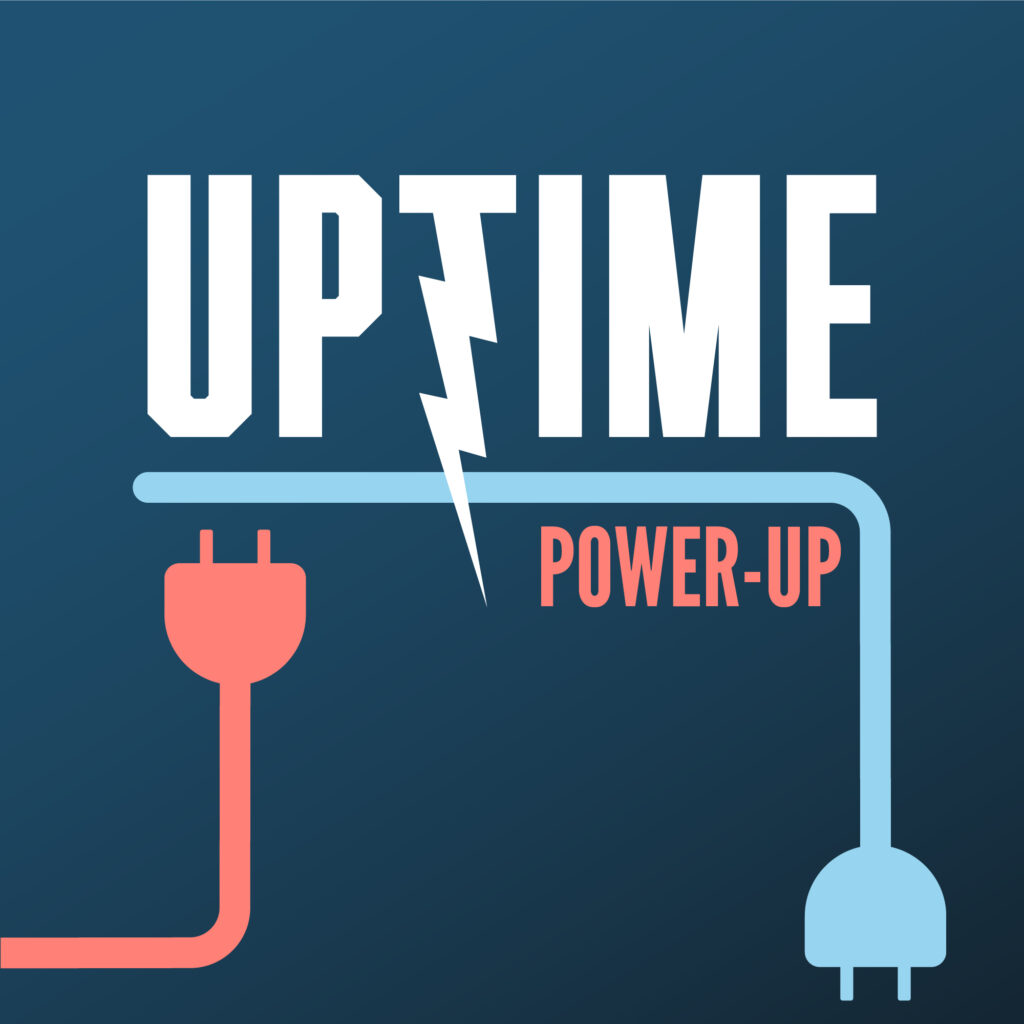
Allen Hall: Welcome to Power Up, the Uptime podcast focused on the new, hot off the press technology that can change the world. Follow along with me, Alan Hall, and idasaur’s Phil Totaro, as we discuss the weird, the wild, and the game changing ideas that will charge your energy future.
Well, our first idea is from Vestas, and it is an idea where they’re monitoring the Turbine tower loads for natural vibration frequency, and you say, well, why would you want to do that? Well, of course, as things change on a wind turbine, maybe something goes wrong. Those frequencies of vibration are going to change, and the system will detect those and say, hey, something is wrong.
Here’s probably what it is, which is a smart way of detecting failure modes in the turbine fill. But the other thing it could do, is push the turbine harder if it’s not being driven hard enough and creating enough power.
Philip Totaro: Yeah, and this is actually really fascinating because, again, this might not sound like the world’s most revolutionary, innovation, but it’s a practical solution to a challenge that is faced out there in the field when you’re operating a wind farm.
And specifically, in addition to just monitoring the, the tower loads and vibration over time, they have the option to monitor the max extreme load in relation to the original design load limit and readjust that max extreme load value over time as there’s an evolution of the, the.
Mechanical performance of, of the turbine. And that to me is, is really clever way of approaching this challenge of having additional safety factor. Or as we see in the United States where turbines get run a lot harder. Than they were potentially designed for. Sometimes because companies are trying to maximize their production tax, credit revenue.
This is a way for a company like Vestus to keep an eye on whether or not they’re exceeding a. Safety criteria, or by how much are you exceeding a safety criteria of, the design load limit versus the max extreme load limit, which will necessarily change over time. As components wear and, and as the tower sees certain load cases on it.
So I, I like this one a lot. I think, again, this is a really practical and clever thing. It might not be, or sound like the world’s most revolutionary. Invention ever, but I, I like stuff like this. This is a really great one.
Joel Saxum: I think it’s a functional way of ensuring the safety and operation of the turbine.
Right. The, the ability to adjust and to understand what kind of loads are being sensed and of course, When we talk about load changes in turbines, it’s every component is completely different, right? The loads in the blades and fatigue loads over time and what can be and can’t be exerted on them. To, to look, like a 20 year old blade is a lot different than a one year old blade and a 20 year old piece of drivetrain is a lot different than a 20, a one year old piece of drivetrain.
So adjusting those load limits by calculation and understanding as the turbine ages and operations change. It’s something that should actually absolutely be done. So I’m, I’m with Phil. I think this is a good one.
Allen Hall: Our next idea is from G. E. in Spain. And G. E. is noted for their two piece blades.
Well, the, the issue with the two piece blade is you want to replace the tip, you have to physically bend it. Get a crane up there and remove the tip. Well, this patent allows the blade tip to be lifted and just, and drop with a cable running through the center of the blade. So it’s sort of a unique way of dropping in a damaged blade tip and putting a new blade tip on.
It has a sort of a coupling mechanism to carry the loads. But Phil, this is a really slick idea. If you’re going to do a two piece blade, the reason you do that, so you can swap out the tip. You need a way to do without involving a crane.
Philip Totaro: Yeah, and, and look, single blade swap outs, an idea that’s been around for like 12 or 13 years or so and has been commercially tested and is commercially used by a few service companies and, and even EPC contractors when they’re doing an initial blade install, they, if they don’t happen to have a crane, they might be able to do the installation of a third blade by using uh, either a turbine based crane or a ground based crane with a winch system that allows you to hook up this harness that’ll, that’ll suck the blade up into the onto the hub.
Now, this invention is for swapping out the tip, which is kind of an interesting use case on a GE Cypress blade, wherein if they happen to have either, let’s say, lightning damage, or some other kind of tip related issue they can literally debolt the I don’t know that they successfully explained how that happens, by the way.
How you get down into the blade deep enough to be able to, unbind the, the joint in there to be able to, to get the tip off. But once you’ve, once you’ve unbinded Unbolted this this tip, doing a quote unquote, single blade swap out with just the tip portion is is certainly a unique approach.
So, assuming that they can resolve some of these other operational challenges and like how you actually, implement this and from a practical standpoint, I think this is, this is interesting. But like we’ve talked about on, Power Up and the Uptime Winnergy podcast before, not everybody’s using a two piece blade and not everybody’s going to use a two piece blade.
So whether or not this patented innovation gets used, universally, we’ll, we’ll have to see.
Joel Saxum: I like anything that can be done without a crane in the wind industry. Without a traditional crane, right? You have the lift draw, the lift works, those guys doing certain things, but something that can be done maintenance wise that traditionally would have taken a crane that you can’t, or that you don’t have to?
Fantastic idea, right? The two piece blades are built for a couple reasons. The main one being logistics and transportation. But the second one is, is that idea that Phil has talked, that talked a little bit about, about the idea behind operations and maintenance of, hey, tip’s got bad leading edge erosion or a bad lightning damage or something, boom, just swap the tip out.
It makes sense from a practical standpoint, however, have we seen it actually happen in the field? Not yet, to my knowledge if anybody has done these things. Please get a hold of us so we can learn a little bit more about it. But yeah, there’s some challenges there because you’re gonna have to probably either use a lift truck to get people up to the joint to remove the they put a seal around it and some other things and, but once, once you get past that, the ability to swap that tip out without a crane is, could be, could be game changing for these
Allen Hall: two piece plates.
Our last idea is a solar powered wind turbine tower, and it’s from Heliotech over in Germany. And the patent idea goes like this. I have this long tower that sits pretty high above the ground. If I can cover that in flexible solar panels, I can generate some electricity. That can go along with the