R&D Test Systems Builds Massive 25 MW Main Bearing Test Facility
Description
In this episode, Peter Winther, Key Account Manager at R&D Test Systems, discusses the construction of the world’s most powerful main bearing test facility at the Lindø Offshore Renewable Center in Denmark. Winther provides fascinating insights into the engineering challenges and scale of this groundbreaking 25-megawatt facility, including details about its massive concrete foundation and the specialized testing capabilities designed to simulate decades of wear in just months.
Sign up now for Uptime Tech News, our weekly email update on all things wind technology. This episode is sponsored by Weather Guard Lightning Tech. Learn more about Weather Guard’s StrikeTape Wind Turbine LPS retrofit. Follow the show on Facebook, YouTube, Twitter, Linkedin and visit Weather Guard on the web. And subscribe to Rosemary Barnes’ YouTube channel here. Have a question we can answer on the show? Email us!
Pardalote Consulting – https://www.pardaloteconsulting.com
Weather Guard Lightning Tech – www.weatherguardwind.com
Intelstor – https://www.intelstor.com
Wind Energy O&M Australia Conference – https://www.windaustralia.com
<figure class="wp-block-image size-full is-resized">
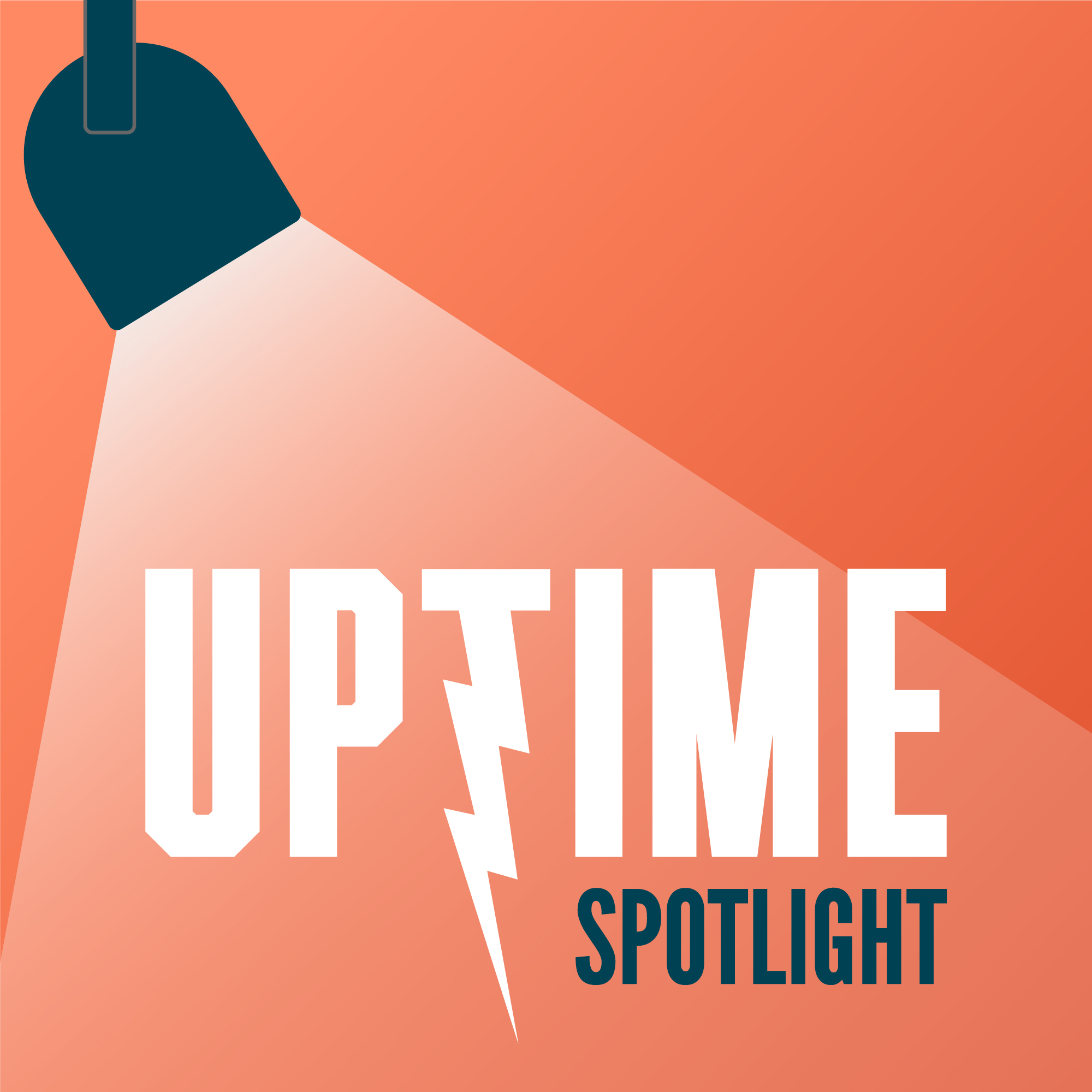
Welcome to Uptime Spotlight, shining light on wind energy’s brightest innovators. This is the Progress Powering Tomorrow.
Allen Hall: Today we’re joined by Peter Winther, Key Account Manager at R& D Test Systems, a company that’s revolutionizing how we test wind turbine components. R& D Test Systems is currently building the world’s most powerful main bearing test facility at the Lindo Offshore Renewable Center in Denmark. They have already delivered the largest halt test bench for nacelle testing at the same location and now these facilities are pushing the boundaries of what’s possible in wind turbine testing with capabilities up to 25 megawatts.
Peter brings extensive experience in large scale test system development and has been instrumental in multiple groundbreaking projects at LORC. Peter, welcome to the show. Thank you very much. Thank you for having me. All right, so you’re building a 25 megawatt main bearing test system. Facility. That’s big.
That’s very big. So just give it a sense of scale. How big is a 25 megawatt bearing?
Peter Winther: The bearing itself, I would guess the inside diameter is more than four meters in a typical bearing constellation. The test bench on the other high, on the other side is also relatively big to be able to break that bearing or bearings, depending on what you’re testing.
The test bench itself pretty big. First of all, features a pretty decent size concrete block or foundation at the bottom, which is roundabout 35 meters long. It took 30 hours to cast the whole thing. It was a one continuous process. We had 280 trucks coming in and they were coming in every six minutes.
And so we basically took all, I think, concrete production from Fyn, which is the island where Ålensø or the test bench is being realized. And then we had back off plants in case the plant went down because if you start casting, you can’t stop, you need to go ahead. You can’t have a cold joint.
Yeah. Yeah. So that’s the foundation itself. An essential thing when you make a foundation like this is also to make sure it cools in the right manner. You can’t just cast it and then go away and then come back in an hour or a week and then all is fine because then you risk not having.
The right material properties throughout the foundation. So we had a more than one megawatt cooling system, making sure that the cross-sectional temperatures throughout different cross sec cross-sections and the foundation was right and not too much of a difference, so we didn’t get cracks and creeping and unwanted properties at the end because you, you can’t really get rid of it.
Allen Hall: When you take this project on, how many engineering challenges are there? Obviously building the. Concrete Foundation by itself is a massive undertaking. How many, how do you break this down and how many big hurdles are there? We’re
Peter Winther: in the lucky position that it’s not, you can say, the first time we’re building a big test rig.
It’s the first time we’re building one that should break a 25 megawatt wind turbine main bearing arrangement. So that’s a first. We have some conceptual building blocks, which we of course relied upon, but it’s, the biggest we’ve ever made. So there’s always challenges. And it’s especially challenging when we need to break something very fast that is at the limit of what is possible to manufacture at this point in time.
There’s a reason why they’re challenged with making 15 or 25 megawatt turbines or whatever they’re saying they can manufacture now. It’s because the, you need also the technology to make bearings sufficiently big enough machining. that you can machine the whole thing. And we need To break something that is intended for 20, 25 years of operation, we need to try to break that in 6 to 12 months.
So it’s a bit of an engineering undertaking to figure out, okay, how do we make our test bench capable of doing that 24 7, also for 20 years.
Allen Hall: I’m curious because you’ve already built a 25 megawatt HALT, Highly Accelerated Lifecycle Testing. At the LORC. And that’s there. So what was the need for a separate facility for the main bearing?
What about main bearings makes the requirements a little bit different?
Peter Winther: You can say in some areas the the 25 megawatt halt, It’s used for validation testing, so that is actually for testing the entire drivetrain, meaning the DUT is an abbreviation we use, device under testing in this case it’s the nacelle.
And for the 25 megawatt HALT test bench, we have already commissioned and there’s an operation over there. It’s also Test the gearbox and the generator which mean we need to be able to apply a pretty significant amount of torque. Also, you wanna stress test the gearbox. Ergo you want to have a lot of torque for the main bearing for the main bearing test bench.
That is not the case. You only have to overcome the friction in the bearings because they don’t see the torque. The torque goes through the main shaft to the gearbox at the back end, in case of a geared solution, and if not, then it’s directly to the generator, but that’s where, why the bearings are there.
So it is actually, It’s overdoing it to test main bearings on the 25 megawatt Holt, because then you pay for a huge direct drive motor in this case, which you don’t need
Allen Hall: in the test. That makes total sense. Okay. And the issues that the industry is having with main bearings is pretty evident and onshore right now there’s a lot of issues in the United States at the moment.
But when we get offshore, that becomes even more critical as 25 megawatt turbines going to repair that gets increasingly difficult. So this is a really key piece of equipment. For offshore wind, isn’t this probably the linchpin to success out on the ocean? It’s at
Peter Winther: least very difficult to change if something goes wrong.
Let’s put it like, everything is difficult to change offshore, but the main bearing arrangement, everything is attached to that in some way, more or less. It’s the connection between the rotating part and the tower. To some extent, so you need to take off a lot of stuff if you are to change the main bearing arrangement or the main bearings.
So yeah, there’s a lot of challenges there and I guess what is evident and what they see is, it is extremely important to test the bearings under the right conditions. What they actually experience in one, in the real life, to get as close to that as possible, which is also what has been the focus.
Focus on this test benches is the main bearing units. We don’t test main bearing standalone, just a bearing, and then turn it around and try to bend it because it is very important, the housing around it, how the loa