Offshore Repair Platform, Adjustable Rotor Shaft, Glowing Tires
Description
This week we discuss Flender’s adjustable rotor shaft assembly, designed to mitigate gear misalignment issues. Then Dolfines’ innovative solution for onsite repairs of floating wind platforms using a telescoping crane. Finally, we highlight Goodyear’s fun and practical glow-in-the-dark tires, which can help locate your vehicle in the dark and add a unique aesthetic touch.
Sign up now for Uptime Tech News, our weekly email update on all things wind technology. This episode is sponsored by Weather Guard Lightning Tech. Learn more about Weather Guard’s StrikeTape Wind Turbine LPS retrofit. Follow the show on Facebook, YouTube, Twitter, Linkedin and visit Weather Guard on the web. And subscribe to Rosemary Barnes’ YouTube channel here. Have a question we can answer on the show? Email us!
Pardalote Consulting – https://www.pardaloteconsulting.com
Weather Guard Lightning Tech – www.weatherguardwind.com
Intelstor – https://www.intelstor.com
<figure class="wp-block-image size-full is-resized">
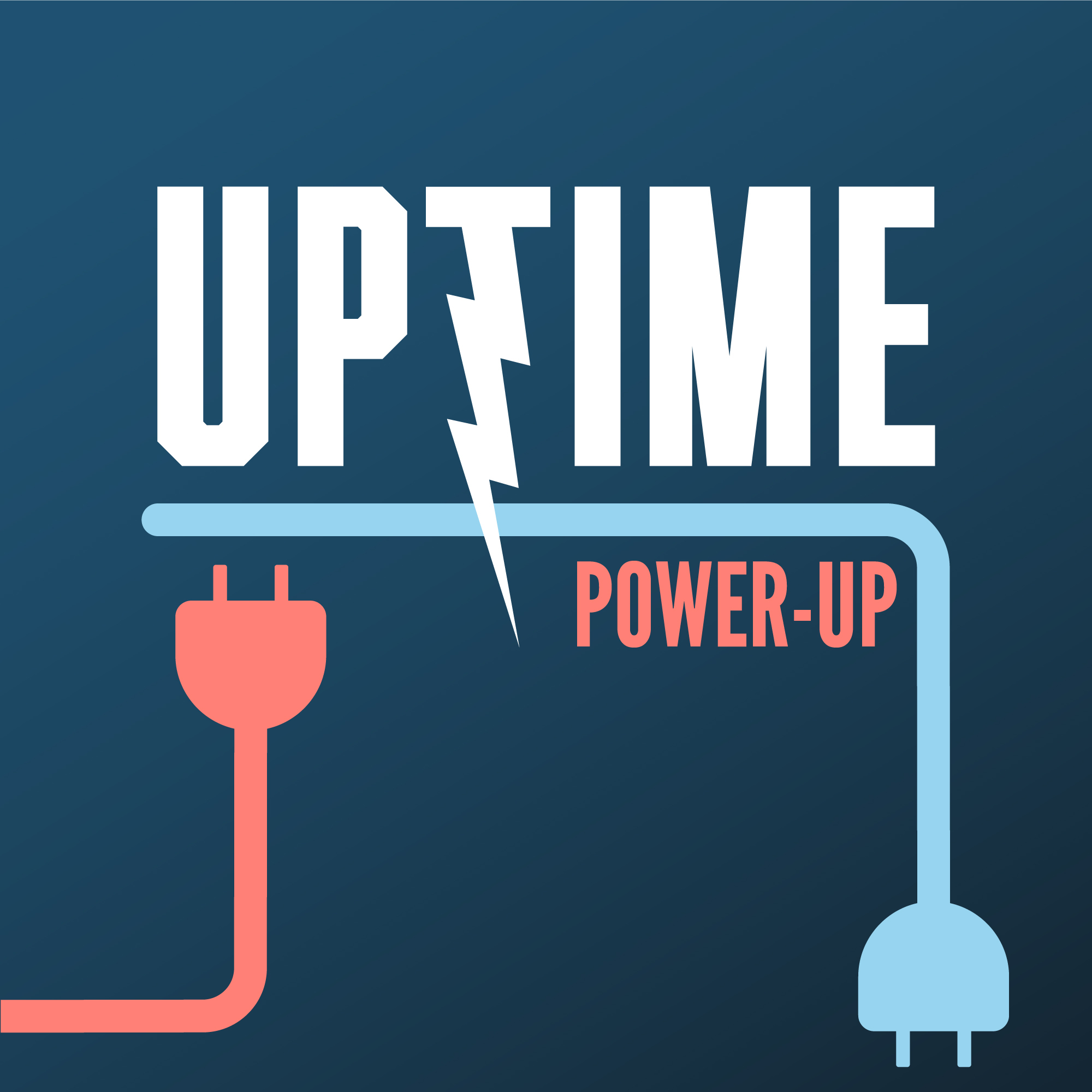
Allen Hall: Welcome to Power Up, the uptime podcast focused on the new hot off the press technology that can change the world. Follow along with me, Allen Hall, and IntelStor’s Phil Totaro, as we discuss the weird, the wild, and the game changing ideas that will charge your energy future.
All right, our first idea of the week is an adjustable rotor shaft assembly for wind turbines. And as we know, there’s all kinds of issues with anything rotating equipment on a wind turbine. Particularly if it involves gears and teeth. Well, this idea from Flender describes an adjustable rotor shaft assembly for connecting a gearbox to the generator.
And the key feature is it uses a curved tooth coupling with the releasable support element which allows the both ends to move relative to one another, which And a lot of wind turbines, if you’ve been up in them, there is a lot of movement at times, and it lets that misalignment not destroy. The assembly.
And this is really slick because we have all kinds of issues, like I’ve said, on anything with teeth, on, on some of these bigger wind turbines as the, the blades get bigger and they get taller and everything’s moving around. Phil, this makes a lot of sense. I’d be surprised if Flinders not using this already though.
Philip Totaro: Yes, I would hope so. We haven’t been able to confirm it, but presumably for the turbines with larger capacity gearboxes for the, the larger onshore machines and maybe even some of the offshore ones. I would hope that this technology is being utilized because it will absolutely help make a difference in kind of bending moment and gear misalignment issues which can create a lot of maintenance work for, for the turbines.
While the services folks may not be happy about it because they might be losing some, losing some revenue opportunities the owners and operators absolutely would love this kind of technology to be implemented because it’s it’s going to allow for a gearbox to be able to, to be operated in a slightly wider loads window which is also kind of an interesting application to this because, even in a market like the U.
S. where we know that a lot of owners and operators are, are kind of PTC farming. They’re not just wind farming. And what that means is they want to be able to extract as much out of the turbine as they can. for the first 10 years of, of an asset life. A technology like this might actually be helpful in making sure that the gearbox lasts the full 10 years before you see any kind of major drop off in performance.
So any technology where you can accommodate this kind of gear misalignment is going to be a good one for owners and operators and, and the gearbox manufacturers themselves.
Joel Saxum: Yeah, I mean, if you have a small rigid component then you can have a fixed gear, fixed location. It’s easy to keep it in line where you don’t have a whole lot of crazy loads on it.
But like, Allen was saying at the beginning of the section here, when you’re bent, if you’ve been up tower at all, these things are moving all over the place. And when you start to get to these larger size turbines and bed plates starting getting really big and things start to flex and move. Having a little bit of basically give in the connections can go a long ways to increasing longevity.
So, it’d be a little bit more of a complicated thing for some, uptower technicians if something goes wrong with it. However, the idea behind the invention is that we won’t have things go wrong. So, this one has some, some good application in the real world.
Allen Hall: Our second idea comes from Dolfines.
And as we know, floating wind is, holds great promise. And, but one of the drawbacks to it is when things go wrong with a turbine, you pretty much have to drag that floating platform all the way back to port and to work on it. And. That can be a problem at times, as we’ve seen recently with some wind turbines over in Northern Europe dragging them back takes a long time as it’s expensive.
So, the Dolfines’ approach is a little bit different where they have a crane on the floating platform and with a telescoping boom on it where they can get access to the blades. So, the way this, this patent idea works is that, They have some handling equipment and they can remove and reinstall blades without the need for any vessels to be out there or the need to tow the floating platform back to port.
This, I think, holds promise, Phil, in that if floating wind is really going to be economical, the turbine size is going to have to get big, but that just increases the complexity, and you really want to repair it on site, putting some sort of crane on the floating platform. Does make sense.
Philip Totaro: Yes. And this, their, their idea is kind of twofold.
As you mentioned, part of it is putting the telescoping crane on the floating platform itself, either if it’s a a, you’re, you’re going to have a bit of trouble if it’s a kind of a spar buoy design, but for, other types of semi submersible arrangements, you can, you can actually have one of the pontoons actually have this this crane embedded but they also have an idea to include this telescopic crane on a jackup vessel as well.
And so the, the core idea of the patent, again, is this telescopic crane, which by itself isn’t necessarily a new idea, but the placement and arrangement of these, and, and again, keep in mind, Dolfines is a oil and gas company that’s got, decades worth of experience in, in Europe in supporting that, that industry.
So they know how to solve problems and their, their solution as far as supporting, floating offshore or even fixed offshore with this kind of, there’s, there’s another company that came up with the quote unquote jackup on a jackup, so we won’t call it that, but the telescoping crane on a jackup vessel is is also a pretty clever way to, to go about it.
So I like it again, keep in mind that this is one they’re not actually using commercially yet, but we think with increasing crane size or with significant deployment of floating offshore platforms, they could. Eventually implement this kind of a solution and, and it’s something I’d actually like to see because it, it would help cut down on, on some, some service and repair costs substantially.
Joel Saxum: When it comes to offshore construction, the two terms that always get thrown around for op enduring operations is coupled or decoupled. So when you talk about a decoupled activity, that would be what we do right now. So you may have a crane on a jackup or on a floating barge or something, go out to where the monopile is in, installed into the seafloor, and those two pieces of infrastructure, the monopile and the vessel are decoupled.
They’re not connected whatsoever. So you have to deal with, movement and moments in both of them. So if the sea settle or the sea floor settles at all, the jackup can move. Or if the, if you get some high currents or something or some wind, you can get the, the monopile can move. And now these two pieces of.
of kit are decoupled. They’re not together. So the